Enterprise 21 ERP System
No Maintenance Fee Increases - Guaranteed. Learn More.The Enterprise 21 ERP application includes complete system administration functionality to support its initial setup and ongoing usage. The Enterprise 21 system’s underlying architecture is flexible and configurable by design. Enterprise 21 has a series of configuration options which allow organizations to enable specific business processes in the system through configuration switches. Additionally, the system’s architecture allows for fast and easy reconfiguration of business processes, allowing organizations to evolve and change their business practices over time to achieve operational gains and a competitive advantage. Read More...
The Enterprise 21 system is built on the principles of management-by-exception. At the heart of this strategy, Enterprise 21 monitors key system processes. When process anomalies occur, the system automatically generates notifications and alerts, which are then sent to individuals or groups for analysis and resolution.
Enterprise 21 supports system-wide security that can be defined globally, by group of users, or on a user-by-user basis. Depending on security privileges, users can access only those functional application areas and screens to which they are authorized. Furthermore, users may be granted the authority to create, update, or merely read the information on individual screens.
In addition to establishing user access privileges, the Enterprise 21 system is easily tailored to provide each user their own unique experience. Enterprise 21 is fully multilingual enabled, allowing users to interact with the system’s menus and messages in their preferred language. Additionally, individual screens and their associated one-touch navigation options can be tailored on a user-by-user basis. Through these capabilities, each individual employee can interact with the Enterprise 21 system in the manner that best meets his or her own preferences.
With Enterprise 21’s robust and flexible system administration capabilities, manufacturing and distribution organizations can tailor the application to meet their unique enterprise software requirements.
No Maintenance Fee Increases - Guaranteed. Learn More.Enterprise 21 is a fully-integrated ERP system for manufacturers and distributors. Enterprise 21 also integrates with third-party applications to support organizations’ complete business needs. The Enterprise 21 system is fully-integrated with the Microsoft Office suite including Word, Excel, Outlook, Exchange, and MapPoint. Read More...
Enterprise 21 is EDI enabled to support customer and supplier EDI transaction processing. Enterprise 21’s flexible architecture allows organizations to use the EDI translation solution that best meets their unique EDI processing requirements.
Enterprise 21 includes hundreds of standard reports and forms that have been developed using Crystal Reports. Through the use of a development license of Crystal Reports, existing reports can be modified and new reports can be created as desired.
To deliver improved customer relationship and order management capabilities, Enterprise 21 integrates with voice over IP (VOIP) technology for one-touch dialing and inbound call routing. Enterprise 21 also integrates with leading online service providers for immediate credit card authorization for sales orders and accounts receivable processing.
Manufacturing and warehouse operations can greatly improve productivity through Enterprise 21’s integration with all leading barcode printing and handheld scanning devices and shipment manifesting systems from UPS, FedEx, and Clippership.
For organizations’ human resources and payroll processing needs, TGI has partnered with ADP. To deliver a route accounting and direct store delivery (DSD) solution for small and mid-market manufacturers and distributors, TGI has partnered with Versatile Systems.
Enterprise 21’s superior functionality and flexible architectural and integration capabilities deliver a complete, cost-effective, and state-of-the-art business software solution to leading manufacturers and distributors.
No Maintenance Fee Increases - Guaranteed. Learn More.The Enterprise 21 ERP system is designed to support a variety of deployment methods and infrastructure options. Enterprise 21 can be deployed in thin-client mode, thick-client mode, or as a combination of these methods using any ODBC-compliant database. Due to Enterprise 21’s scalable design, small and mid-market manufacturers and distributors can implement and continue to run Enterprise 21 as their businesses grow and evolve over time. Read More...
Deployment Methods
Manufacturers and distributors can access Enterprise 21 in a variety of methods including thin-client mode, where the system would run on an application server; thick-client mode, where the system would run directly on desktop and laptop computers; or as a combination of these approaches. The system can also be accessed via the Internet or deployed in a Software-as-a-Service (SaaS) model.
Database Options
The Enterprise 21 ERP software suite can be deployed with any ODBC-compliant database. Most commonly, TGI’s customers elect to deploy Enterprise 21 on Microsoft SQL Server, Informix, Oracle, or IBM DB2. The chosen database management system can be run on any associated supported database server technology, including Microsoft Windows, UNIX, Linux, or IBM OS/400.
Application Options
In thin-client mode, organizations would typically run the Enterprise 21 system on Windows Server-based application servers. Application access can be performed by any device which can connect to and run applications on these servers through a browser or remote desktop connection. Typical access devices include Windows-based systems, Mac OS-based systems, thin-client appliances, and mobile devices. In thick-client mode, Enterprise 21 runs on Windows-based and Mac OS-based devices.
Ad-hoc reporting refers to the ability of users to produce their own customized reports on an as-needed basis. TGI uses Crystal Reports for the development of standard reports and forms. Enterprise 21 includes several hundred predefined reports which can be run with standard selection criteria. Enterprise 21’s also includes standard forms such as purchase orders, invoices, pick lists, packing slips, bills of lading, sales quotes, and order acknowledgements. Read More...
Through the use of a development license of Crystal Reports, existing reports can be modified and new reports can be created. These modified and new reports can be added to the Enterprise 21 system library without changing application source code and can be run just like any of the standard reports.
TGI customers can access and review real-time business information through the inclusion of standard reports, forms, and ad-hoc reports.
Watch the Enterprise 21 Workbenches DemoEnterprise 21’s workbench technology allows for a personalized workspace environment that can be uniquely defined by TGI customers and software users. Workbenches are consolidated views of information in Enterprise 21 where a variety of associated data can be easily accessed. Workbenches can be defined by TGI customers without modifying application source code and can consist of data viewable in both tabular and graphical formats. Read More...
Given users can create their own workbenches to manage their workday via one convenient screen with ease and efficiency. From the personalized workbench, the user can quickly navigate to all other areas in the system to perform transactions, run reports, or drill down to more detailed data.
A sales representative or sales manager’s workbench, for example, could include pending activities, pipeline reports, quota attainment, and virtually any other data that resides within the Enterprise 21 application. Enterprise 21’s workbench technology is intended for all functional areas including customer service, production planning, production operations, procurement and sourcing, warehouse operations, financial management, and a variety of other areas.
Watch the Enterprise 21 Business Intelligence DemoKey performance indicators, or KPI’s, are scorecards that provide summarized information regarding an organization’s current attainment against its established organization-wide goals and objectives. KPI’s provide management and individual employees with visibility to key data including overall profitability against plan, customer service index, and organization-wide inventory performance. Read More...
KPI’s can be used to focus all personnel on common objectives and have ongoing visibility to organization performance. TGI customers can deploy their organizational KPI’s through Enterprise 21’s business intelligence dashboards via a variety of graphical charts and gas gauges.
Watch the Enterprise 21 Business Intelligence DemoEnterprise 21’s business intelligence dashboards are designed to make decision support technology easy to use, easy to deploy, and affordable. Enterprise 21’s dashboards provide a consolidated view of data pertinent to the given user’s role within the organization. Read More...
Enterprise 21’s business intelligence solution includes a dashboard environment unique to each user featuring reports, graphs, tables, and alerts. This allows users at any organizational level to have key performance indicators that are specific to their job function.
Executives, for example, can view information such as up-to-date financial reports, key performance indicators, organization-wide inventory data, sales and margin by product line, and external data such as commodity prices and leading economic indicators. In addition, business unit managers can review inventory turns per year, day supply on hand, order and line-item service level performance, and financial data specific to their given business unit. Furthermore, a customer service or sales representative can view information such as open sales quotes, open orders, sales history, and outstanding accounts receivable position by customer.
Enterprise 21’s dashboards offer a seemingly unlimited list of analytical possibilities.
Watch the Enterprise 21 Business Intelligence DemoEnterprise 21 includes a fully-integrated decision support system that provides robust executive information system functionality without the need for third-party solutions and associated data migration. Read More...
Enterprise 21 allows users to select from a series of standard reports across all functional areas. Users can drill-down on the data in these reports across a series of data elements called dimensions. Dimensions can include elements such as organizations, products, customers, geography, and time with the data filtered based on the desired criteria. Data can be viewed in graphical and chart formats which can be modified by selecting the desired format. Reports and data can be exported directly to Microsoft Excel for further manipulation.
Enterprise 21 transactional data automatically feeds the decision support system and includes embedded structures such as customers, products, and the company’s organization. Enterprise 21 provides information to all levels of management and knowledge workers and ensures that users throughout the organization see the same information at any given point in time. This provides the overall organization a single version of the truth.
Enterprise 21’s service and support functionality provides a mechanism to perform help desk support for manufacturing and distribution organizations. Enterprise 21 ERP software’s help desk features provide an efficient means of tracking support calls from inception, to routing of the issue to a service technician, through problem resolution. The service and support functionality is fully-integrated with the rest of the Enterprise 21 software suite so key information such as order history, serial numbers, and warranty information are quickly available for support personnel. Read More...
Service Management Highlights
- Supports creation of an issue, assignment to personnel, and documentation of resolution
- Supports issue date and time stamps for opening and closing to calculate elapsed time to resolution
- Allows entry of issue categories and prioritization
- Supports product serial number and warranty or maintenance tracking
- Supports associated generation of a product return
- Online visibility to data enables root cause analysis
Watch the Enterprise 21 CRM DemoEnterprise 21’s fully-integrated CRM solution helps connect marketing, sales, and customer service personnel by integrating prospect and customer sales activity with the marketing department’s communication and campaign efforts. From demographic analysis and campaign tracking to lead generation and conversion to sales, Enterprise 21’s CRM software delivers a cohesive solution designed to increase sales and customer satisfaction. Read More...
Marketing Management Highlights
- Allows definition of a four-level hierarchy for prospects and customers for groups or segmentation
- Supports customer and prospect buying preferences, interests, and other relevant demographic data
- Supports creation and tracking of marketing campaigns with contact-specific flags for campaign inclusion
- Supports sending of mass emails to prospects and customers based on buying preferences and customer demographics
- Supports email template definition for quick and easy communication
- Tracks lead source for prospects and opportunities
- Supports importing of external contact databases and lists
- Generates mailing labels and form letters via mail merge
- Tracks competitor data for competitive bid analysis
Watch the Enterprise 21 CRM DemoEnterprise 21’s fully-integrated CRM solution provides a telemarketing and lead management system designed to optimize the productivity of your inside sales team. Enterprise 21 includes mass call scheduling, VOIP auto-dialing functionality, call activity recording, and inbound call routing. Enterprise 21 CRM software also includes lead distribution, pre-configured mail merge documents and e-mails, customizable reports, and graphical dashboards. Enterprise 21 delivers the CRM functionality needed to optimize your organization’s sales performance. Read More...
Telemarketing Management Highlights
- Fully integrated with VOIP for one-click dialing
- Enables mass call scheduling using a variety of selection criteria
- Supports a daily activity listing by user and results reporting
- Supports automated workflow aligned with process specifics
- Provides visibility to sales performance results in graphical and tabular formats
The Enterprise 21 ERP software solution provides integrated functionality for managing and tracking sales commissions and incentives programs and processing associated payments. Enterprise 21’s commission management solution supports multiple commission methodologies. Commissions can be paid at invoicing or deferred until customer payment is received. Enterprise 21’s ERP software makes calculating and reporting sales commissions simple and straightforward. Read More...
Sales Commission Management Highlights
- Allows comprehensive commission structures based on sales revenue, margin, and quota attainment
- Split commissions can be calculated at multiple levels of sales activity
- Commission overrides can be defined by customers, products, sales types, or in combination
- Commissions can be paid at invoicing or receipt of payment from customer
- Supports online visibility of commissions and quota attainment by sales reps and managers
Watch the Enterprise 21 CRM DemoEnterprise 21’s CRM software serves as a virtual sales assistant and provides an automated tool for helping sales representatives increase productivity and revenue. Enterprise 21 streamlines manufacturing and distribution organizations’ sales activities into one centralized, cohesive software solution. Read More...
The Enterprise 21 ERP solution includes complete sales force automation functionality which tracks incoming sales leads and opportunities, monitors pending activities, tracks ongoing communication, and displays the sales pipeline in graphical and tabular formats. In addition, Enterprise 21’s CRM software is fully-integrated with the rest of the Enterprise 21 ERP software suite providing a comprehensive view of organization-wide information, including quotes, pricing, and order management.
Sales Force Automation Highlights
- Supports territory management
- Commission management
- Enables sales force automation including automated workflow processing, activity management and automated reminders, and sales call tracking and reporting
- Supports lead management and opportunity tracking across the entire sales pipeline
- Revenue forecasting
- Online quoting and proposal management
- Tracks competitor data for competitive bid analysis
Watch the Enterprise 21 Financial Management DemoEnterprise 21 ERP software provides complete audit support by ensuring that all transactions and database changes are properly authorized and processed. In Enterprise 21, every screen can be flagged as auditable and can be defined as such by an easy to use system administration table. Read More...
Audit Trails Highlights
- Audit trails are available in detail for both internal and external auditing
- Audit trails are available for master tables and transaction records
- The general ledger provides complete recording, integration, and detailed audit controls by accounting entity
- Audit trails are available to support tracking of general ledger account balances to source transactions
- Audit trail generates a report of all accruals and reversals
- Audit trail generates a report of purchase order history and applicable electronic signature approvals
Watch the Enterprise 21 Financial Management DemoThe Sarbanes-Oxley Act of 2002 focuses on the proper management and disclosure of corporate financial information. Enterprise 21 ERP software automates the documentation and control of transactions and processes in compliance with Sarbanes-Oxley or SOX regulations. In doing so, Enterprise 21 provides the basis for financial reporting required by financial and executive management and external auditors for compliance purposes. Read More...
Sarbanes-Oxley (SOX) Highlights
- Secure system user login and tracking
- Segregation of duties via multi-level system security
- Transactions are recorded and accounted for accurately
- Online support of corporate policies and procedures
- Online approvals and authorization for transactions
- Controlled reporting of financial data
Watch the Enterprise 21 Financial Management DemoEnterprise 21 financial management software supports organizations in their compliance efforts through multi-level security with segregation of duties by user, integrated workflow management, and complete master file and transaction audit trails. Enterprise 21 integrates multiple entity companies into a single system and database image, thus providing one central repository of master files, transactions, and their associated audit trails. Read More...
With the help of Enterprise 21, the information technology and accounting departments become a unified internal audit team that facilitates and supports corporate responsibility, accountability, and compliance activities. This integrated approach to data management provides the backbone of compliance reporting for financial and executive management and external auditors.
As part of Enterprise 21’s financial management solution, corporations can elect to manage and perform accounts payable and accounts receivable at a corporate level via the corporate cash management functionality. In doing so, the associated accounts payable or accounts receivable transactions roll up to the higher-level business entity, where the actual payment or posting of cash processes take place respectively. Enterprise 21 also reflects the completion of processing for the detailed transactions at the lower-level business entity and manages the associated intercompany financial transactions in accordance with GAAP standards. Corporate cash processing can be a critical element for executing timely payments and optimizing a corporation’s overall cash management position.
Enterprise 21 improves organizational accountability by strengthening the accuracy of the corporations’ budget activity and by providing online visibility to actual performance against projected budgets. This improvement in budget management is accomplished by utilizing Enterprise 21’s historical data to create concise, accurate budgets for management review and adjustments where needed. Enterprise 21 generates multi-level budgets for standard sales cycles and seasonal patterns, and supports the entry of manually created budgets. This fully-integrated approach provides a centralized view of multiple-entity budgets, significantly reduces data integrity issues, and improves overall budget accuracy. Read More...
Budget Management Highlights
- Supports a base budget, current budget, and infinite working budgets per fiscal year
- Budgets can be generated from existing historical data in the system
- Budgets can be updated by values or percentages within individual periods, or on overall top-line values spread to corresponding periods
- Supports accessibility to historical prior year budgets
- Multiple budgets can be created to perform what-if analysis (best case, worst case, most likely, etc.)
- Reporting can be performed on actual vs. budget across any combination of one or more of the base, current, and working budgets at a detail or summary-level
- Increases or decreases overheads by entering a percentage for specific accounts or for groups of accounts
- Supports online display of actuals to budget
- Reports can compare multiple years’ actual and budgeted amounts
Enterprise 21 offers sales tax management to help control tax-related transactions and mitigate risk. Enterprise 21 supports sales tax calculations at multiple levels and locations while also supporting the necessary variations to accommodate business activities in multiple countries. Enterprise 21 also integrates with external tax packages to provide the optimum solution for management and reporting of tax liability and expense. Read More...
Tax Management Highlights
- Stores customer tax codes by customer bill-to address and ship-to locations
- Stores customer tax exemption certificates for all levels
- Allows separate tax status by product for product purchases and sales
- Supports tax calculations by country, state or province, county, city
- Posts sales tax to user-specified account
- Supports 1099 and W2 reporting and form printing
- Reports intercompany sales for reporting and tax purposes
- Supports integration of external tax packages
Enterprise 21’s financial management provides strong support for bank management that extends across the general ledger, accounts payable, and accounts receivable functions. Enterprise 21 allows the entry of multiple bank accounts each of which can have a unique base currency to support organizations ranging from a single business entity to multiple legal entities across one or more countries. Bank reconciliation can be performed manually or in an automated manner utilizing an electronic feed from the customer’s given financial institution. Read More...
Bank Management Highlights
- Supports multiple bank accounts, with each account having its own base currency
- Supports receipt of an electronic feed for automated bank reconciliation
- Allows manual reconciling by range of checks
Watch the Enterprise 21 Financial Management DemoEnterprise 21 ERP software includes an easy to use financial report writer designed to help organizations effortlessly produce financial reports directly from Enterprise 21. The financial report writer automatically delivers data from the general ledger into Excel-based templates. This process enables the financial management team to produce and share professional financial reports customized to an organization’s unique reporting requirements. Read More...
Financial Report Writer Highlights
- Automatically generates financial reports by combining select Enterprise 21 financial data with predefined templates in Microsoft Excel
- Generates customized balance sheets, income statements, profit and loss statements, financial ratios, cash flows and other financial reports
- Easily filters financial reports by any business segment, such as department, cost center, division, or company
- Simplifies financial consolidation review and comparisons
- Provides significant flexibility by allowing users to produce financial reports that span any time period
- Allows users to report period-to-date, year-to-date, year-to-year, and actual vs. budgeted financial data
- Financial reports can be automatically generated and displayed in executive dashboards
Watch the Enterprise 21 Financial Management DemoEnterprise 21’s integrated financial management software manages multinational operations and multicurrency transactions with exchange rate updates and currency conversions. Enterprise 21 provides a variety of exchange rate options to support efficient processing while complying with GAAP. In addition, Enterprise 21 automatically determines unrealized gain or loss due to currency rate fluctuations and restates financial information at the new exchange rate. Read More...
Multi-Currency Highlights
- Manages multiple currencies for transactions, accounting, and financial reporting
- Exchange rates may be pulled into the system from an automatic data feed or entered manually
- Supports multiple currency conversion application types such as daily, monthly, annual
- Supports conversion factors to be used for financial report generation
- Revalues foreign currency accounts and automatically determines gain or loss due to currency fluctuations
- Automatically restates, at a new exchange rate, consolidated multi-currency financial information
Enterprise 21 ERP software provides strong cost accounting and financial management by tightly monitoring and tracking all cost elements of a given product whether manufactured or purchased. Enterprise 21’s cost accounting generates accurate costing and performance information, providing improved visibility to the organization’s financial opportunities to reduce excessive cost elements and increase profitability. Read More...
Cost Accounting Highlights
- Supports multiple costing methods including standard, FIFO, LIFO, and average costing
- Costing method may be specified by individual product or SKU
- Cost components include material, labor, and burden or overhead
- Costs can be rolled up from lower levels of the bill of material or formulation to higher levels
- Tracks multiple costs per item
- Supports multiple methodologies for the allocation of overhead
- Supports standard versus actual comparison within associated posting to the general ledger
- Maintains multiple costing layers for WIP and finished goods
- Supports methods for revaluing or recosting inventory
- Can perform what-if analysis and roll costing simulations in as updated product costs
- Tracks cost of inventory transferred between company and divisions
- Supports complete audit trail for transaction records
Enterprise 21’s ERP software has fully-integrated returns and debit processing. This process links the purchasing, inventory management, and accounts payable functions to create a streamlined flow of information for efficient and error-proof transactions. Read More...
Vendor Returns and Debit Memos Highlights
- Fully integrated with the purchasing, inventory management, and accounts payable functions
- Vendor returns can be created automatically as a result of a customer return and subsequent receipt in the warehouse
- Provides the user the ability to tie a return to a specific purchase order
- Provides return reason codes for vendor performance analysis
- Returns can generate a credit or vendor re-shipment
- Supports the generation and application of debit memos
Enterprise 21’s accounts payable processing provides automated support for vendor rebates. This process manages and tracks vendor rebates by a percentage or currency value and can associate a rebate with a given customer account. Rebates can occur for an individual product or group of products. Enterprise 21 automatically calculates the accrued rebate and provides online review, reporting, and efficient rebate check processing. Read More...
Vendor Rebates Highlights
- Supports rebates for any combination of individual products, product groups, or individual customers
- Calculates rebates by percentage or currency value
- Supports rebates by contract effectivity dates
- Tracks year-to-date sales and associated rebate amounts
- Supports rebate check processing
Enterprise 21’s accounts payable processing supports the selection of unpaid vouchers for payment, payment processing, and posting to the appropriate source journal. Enterprise 21 supports payment by check, eCheck, ACH, and EFT. In addition to flexible check preparation and printing and the creation of electronic feeds for paperless payment processing, Enterprise 21 supports voiding of single or multiple checks while providing a complete audit trail. Read More...
Payment Processing Highlights
- Enables flexible payment of invoices based on various selection criteria
- Supports multiple bank accounts
- Supports multiple currencies
- Supports manual check creation
- Supports payment by check, eCheck, ACH, and EFT
- Verifies that checks were written by approved personnel only
- Supports check voids by single check or by range of checks
- Supports printing of replacement checks
- Provides a complete audit trail
Enterprise 21’s invoice processing provides efficient management, reconciliation, and payment of invoices. This functionality offers the accounts payable team real-time information and a means to review the purchase order, associated receipts, and invoice, and resolve any discrepancies. This automated process provides both two-way and three-way matching to reduce processing time and data errors, and eliminate over payments. Read More...
Invoice Processing Highlights
- Supports both two-way matching and three-way matching
- Supports online routing and approval of invoices
- Places an individual vendor, individual invoice, and individual line on hold
- Tracks payment and discount information
- Supports sales tax processing
- Supports default currency
- Scans and stores scanned invoice images for online viewing
- Supports credits and adjustments
- Links cost adjustment back to original invoice and payment
- Calculates purchase price variance
- Supports recurring vouchers
- Supports periodic expenses
Enterprise 21’s accounts payable functionality provides an online voucher system that applies a controlled set of processes in a flexible yet effective manner. This automated process manages purchases and payables in a timely fashion and facilitates efficient operations, reduces data errors, enhances financial visibility, and improves cash flow.Read More...
The accounts payable solution supports a multi-level company structure, multicurrency transactions, multiple bank accounts, corporate cash accounting practices, and electronic funds processing. These transactions feed the general ledger via the accounts payable source journal. Accounts payable data is available for flexible reporting through Enterprise 21’s workbenches and dashboards.
Enterprise 21’s manages credit and collections in a real-time, efficient manner through the use of online financial information and an integrated collection call log. Accounting personnel have online access to critical information such as customer balances, outstanding invoices, receivables aging, and key financial statistics. This information arms the collections agent with the data necessary to resolve issues and obtain customer payments. Read More...
Credit and Collections Highlights
- Provides central control over credit policy information
- Provides online access to customer credit limit, payment history, and collection notes
- Supports the placement of sales orders on credit hold based system criteria and user hold based on company policies
- Supports standard dunning notices and associated history
- Provides automated collection calls with customer information, associated notes, and follow-ups
Enterprise 21’s invoicing processing creates accurate invoices that include calculation of charges for products, services, freight, and sales tax while also managing commissions, discounts, allowances, and rebates. Invoices are generated in the customer’s default currency and formatted to their unique requirements. These transactions are then posted to the appropriate source journal in the general ledger, providing a complete audit trail from the invoice to the original sales order and associated shipments. Read More...
Enterprise 21 cash application supports automated processing of electronic bank feeds, as well as flexible manual cash application through a host of inquiries and invoice groupings. Enterprise 21 also supports corporate cash application, allowing cash application to be performed at an enterprise-wide level for a combination of business units and divisions.
Invoice Processing and Cash Application Highlights
- Unique invoicing methods and invoice print formats can be specified by customer
- Invoices can be generated and grouped by sales order, customer PO number, or customer account
- Customers can be invoiced on regular intervals that include daily, weekly, or monthly
- Apply cash to a customer account based upon multiple criteria to one or multiple invoices
- Online review of each customer’s account status with payables trending over time
- Automated cash application using electronic bank feeds
- Corporate cash application process allows cash application to be performed at an enterprise-wide level for a combination of business units and divisions
Enterprise 21 ERP software supports flexible payment options to accommodate both traditional and online order placement. Enterprise 21 provides efficient customer payment processing including cash payments, online credit card processing, discounted terms, installments, or any combination of payment methods. Read More...
The Enterprise 21 ERP software suite includes integration to major credit card gateways. This fully-integrated process provides the ability to pre-authorize a customer’s purchase against their credit card during order entry and confirm the charge at invoicing. Enterprise 21’s enables efficient payment processing while delivering superior customer service.
Payment Methods Highlights
- Supports multiple methods of payment including cash, credit card, and EFT
- Stores encrypted credit card information for multiple cards per customer
- Credit cards are pre-authorized during order entry and charged at invoicing
- Supports an infinite set of on-account payment terms
- Payment terms can be a combination of terms, such as cash down payment with specified percentages paid over defined time frames
Enterprise 21’s accounts receivable functionality strengthens the order-to-cash process flow by providing a controlled yet streamlined approach to billing and payment processing. This fully-integrated solution offers the utmost in flexibility and efficiency for Enterprise 21 software users. Read More...
The accounts receivable processing is fully integrated with rest of the Enterprise 21 software solution, allowing an organization to share information with customer service and sales personnel. In addition to strong multicurrency and customer pricing capabilities, Enterprise 21 includes a credit and collections process to enhance overall customer service and cash flow.
Watch the Enterprise 21 Financial Management DemoEnterprise 21’s financial management functionality enables flexible and automated period and year end processing. Enterprise 21’s financial management solution allows for each business’ unique fiscal period definition. One can have an infinite number of periods open at any time, and with appropriate security privileges, closed accounting periods can be reopened for making correcting entries. Once these correcting entries are made, adjusted balances are rolled forward without the need to reopen other previously closed accounting periods. Read More...
Unlike other systems, Enterprise 21’s general ledger includes a fiscal year definition such that business processing can occur in a new fiscal year without closing and zeroing out values in the prior fiscal year. This capability allows companies to run year end processing multiple times while ensuring transactional integrity in the new business year.
Period and Year End Processing Highlights
- Flexible, user-defined accounting period definition
- Source journals can be closed independently
- Supports multiple periods open at one time and allows transactions in the next period even though the previous period is not closed
- With appropriate security privileges, previously closed periods can be reopened to make correcting transactions
- Year end processing can be performed multiple times as necessary
- Supports fiscal year definition within the general ledger so processing can occur in the new fiscal year while finalizing processing within the prior year
Watch the Enterprise 21 Financial Management DemoEnterprise 21 ERP software provides a flexible, multi-level general ledger structure that supports such entities as multiple companies, business units, divisions, facilities, departments, or profit centers. These relationships are easy to define through a flexible process that allows an organization to modify or expand the account structure as needed. In addition, Enterprise 21’s built-in financial report writer automatically generates professional financial statements at any level of the organization desired. Read More...
Multi-level Chart of Accounts Highlights
- Track multiple organizational segments such as companies, business units, or profit centers
- Hierarchy of departments can be consolidated by levels for summary purposes
- Financial data can be viewed at various levels of the overall business hierarchy
- Financial reporting can be performed at multiple organization levels, from a department or facility through company and business unit to an overall consolidated enterprise
- Various legal entities can each operate with their own base currencies while being consolidated into a common corporate currency at an overall enterprise level
Watch the Enterprise 21 Financial Management DemoThe Enterprise 21 general ledger offers a flexible chart of accounts combined with a series of source journals that support multi-level account definition and consolidation with real-time access to overall cash flow and profitability. In addition, the general ledger supports flexible period definition, automated period end processing, and is completely multicurrency-enabled. Enterprise 21’s general ledger supports manual, recurring, and reversing journal entries, and allocations. Read More...
Enterprise 21’s general ledger provides strong audit support with drill-down capability, allowing for retrieval of all data from a summary level down to detailed transactions. Data can be exported to the integrated financial report writer. These capabilities provide a fully-integrated financial management solution for a wide range of manufacturers and distributors from small start-up companies to multinational, publicly-traded corporations.
In Enterprise 21, production schedules, consisting of a series of work orders, can be created manually and generated automatically. To generate the tentative production schedule, organizations establish a master production calendar which defines hours of operation by day and shift and the associated labor pool that will be available during those times. Read More...
Through the MRP process, tentative production scheduling is capacity-constrained, and is generated based on material, machine, and labor availability. The tentative production schedule can be reviewed by manufacturing planners and changed as desired. The tentative production schedule’s suggested work orders can be rescheduled and resequenced. The tentative production schedule can then be converted in part or in whole to the final production schedule. Both the tentative and final production schedules can be viewed in either a graphical or tabular format by machine, process, or entire facility.
As the business day transpires, the graphical view of the final production schedule updates with color-coded alerts, highlighting issues that may occur based on delayed and out-of-spec production process rates. The final production schedule’s associated work orders are used on the shop floor for production reporting purposes.
Production Scheduling Highlights
- Production schedules can be created manually and generated automatically
- Tentative production schedules are generated based on a master production calendar
- Master production calendar defines hours of operation by day and shift and associated available labor pool
- Tentative production scheduling is capacity-constrained, and is generated based on material, machine, and labor availability
- Tentative production schedule can be reviewed and changed as desired
- Work orders can be rescheduled and resequenced
- Tentative production schedule is converted in part or in whole to the final production schedule
- Both the tentative and final production schedules can be viewed in either a graphical or tabular format by machine, process, or facility
- Final production schedule updates with color-coded alerts, highlighting issues that may occur based on delayed and out-of-spec production process rates
- Final production schedule’s work orders feed shop floor production reporting
Watch the Enterprise 21 Forecasting & Planning DemoEnterprise 21’s material requirements planning (MRP) functionality ensures raw materials, ingredients, and packaging supplies are available for production, to readily meet customer order requirements while optimizing inventory levels for improved discrete and process manufacturing efficiency. Read More...
Enterprise 21’s material requirements planning (MRP) software functionality performs time-phased requirements planning for single and multi-facility manufacturing organizations. This process calculates inventory requirements over time and automatically generates online purchase requisitions and tentative production schedules, which can be turned into purchase orders, inventory transfers, and final production schedules.
To generate the tentative production schedule, the MRP process uses customer demand in the form of sales orders and forecasts, inventory levels and associated replenishment methodologies, multi-level bills of material, routings, available production capacity, and supplier information such as lead times and purchase order requirements.
Furthermore, Enterprise 21’s MRP process calculates expected inventory levels over time and generates purchase requisitions with appropriate time offsets to meet future projected inventory shortfalls. Buyers and material planners can review the purchase requisitions and automatically generate the necessary purchase orders and intercompany transfers to support the organization’s inventory plan.
Enterprise 21’s manufacturing software functionality enables discrete, process, and mixed-mode manufacturers to generate purchase requisitions, tentative production schedules, and real-time alerts and notifications to create the material plan necessary to fulfill customer demand efficiently.
Material Requirements Planning (MRP) Highlights
- Performs time-phased requirements planning for single and multi-facility manufacturing organizations
- Generates online purchase requisitions and tentative production schedules
- Uses customer demand in the form of sales orders and forecasts
- Uses inventory levels and associated replenishment methodologies
- Uses multi-level bills of material, routings, and available production capacity
- Uses supplier information such as lead times and purchase order requirements
- Calculates expected inventory levels over time and generates purchase requisitions with appropriate time offsets to meet future projected inventory shortfall
Watch the Enterprise 21 Forecasting & Planning DemoEnterprise 21’s distribution requirements planning (DRP) software functionality performs time-phased requirements planning for single and multi-facility distribution organizations. This process calculates inventory requirements over time and automatically generates online purchase requisitions, which can be turned into purchase orders and inventory transfers. Read More...
Enterprise 21’s DRP process uses customer demand in the form of sales orders and forecasts, inventory levels and associated replenishment methodologies, and supplier information including lead times and purchase order requirements. Through the DRP process, Enterprise 21 calculates expected inventory levels over time and generates purchase requisitions with appropriate time offsets to meet future projected inventory shortfalls. Buyers and material planners can review the purchase requisitions and automatically generate the necessary purchase orders and intercompany transfers to support the organization’s inventory plan.
For multi-facility organizations, Enterprise 21’s DRP process can be used for centralized purchasing, facility-based purchasing, or as a combination of these methodologies. Enterprise 21’s distribution software functionality allows distributors to meet their inventory planning requirements while effectively managing inventory carrying costs.
Distribution Requirements Planning (DRP) Highlights
- Supports time-phased requirements planning for single and multi-facility distribution organizations
- Calculates inventory requirements over time and automatically generates online purchase requisitions
- Uses customer demand in the form of sales orders and forecasts
- Considers current inventory levels and associated replenishment methodologies
- Evaluates supplier information including lead times and purchase order requirements
- Calculates expected inventory levels over time and generates purchase requisitions
- Support the organization’s inventory plan
- Supports online review of purchase requisitions and automatic generation of purchase orders and intercompany transfers
- Supports centralized purchasing, facility-based purchasing, or a combination of these methodologies
Watch the Enterprise 21 Forecasting & Planning DemoEnterprise 21 ERP software includes a sophisticated demand and sales forecasting software solution. Manufacturing and distribution organizations can manage an infinite number of forecasts in Enterprise 21, which can be entered manually or automatically generated through a series of algorithms to determine anticipated future demand on a product-by-product basis. Once created, forecasts are used as inputs to Enterprise 21’s material requirements planning (MRP) and distribution requirements planning (DRP) processes. Read More...
A variety of different data dimensions are available for sales and demand forecasting. These include break-outs of data by:
- Geography – from as detailed as 9-digit postal codes to as aggregated as user definable regions
- Time periods – from as detailed as a day to as aggregated as a year, with up to 365 different periods in any forecast
- Customers – from as detailed as an individual customer ship-to location through any one of four additional user-defined customer hierarchal aggregate levels
- Products – from as detailed as an individual SKU through any of four additional user defined product hierarchal aggregate levels
In addition, each individual forecast can be generated using a different date range of historical information. Enterprise 21’s sales forecasting software functionality is capable of utilizing more recent sales trends rather than long term trends.
Each time a forecast is generated, Enterprise 21 runs a series of statistical forecasting algorithms and determines which of the various demand and sales forecasting methods represents the best fit to the historical data. It then chooses this forecasting technique to project future demand. As a result, a number of different forecasting techniques may be utilized in a given forecast since the best forecasting technique is chosen for each product, customer, time period, and geographical data combination.
Enterprise 21’s machine maintenance software functionality provides the ability to track machine maintenance intervals and be notified when a given machine requires maintenance. Maintenance management allows for the establishment of machine component lists and associated mean-time between failure (MTBF) standards, creation of standardized procedure lists, and the association of procedures and maintenance documents to specific machines and processes. Enterprise 21’s production scheduling and maintenance management functionality are fully integrated, thus allowing for time to be reserved on the production schedule for preventative maintenance activities. In addition, plant floor personnel can immediately initiate machine maintenance in the event of machine anomalies and downtime. Read More...
Machine Maintenance Highlights
- Supports preventive or scheduled maintenance and non-planned or on-demand maintenance request
- Downtime resulting from scheduled equipment maintenance activities is included in production scheduling activities
- System notifications of preventive maintenance orders which require machine downtime
- Supports entry of a machine BOM or equipment part list and on-line maintenance instructions
- Supports creation of maintenance work orders and scheduling of associated maintenance labor requirements
- Plans purchases of MRO items, which are managed in inventory and consumed by maintenance activities
Good Manufacturing Practices (GMP) refers to an organization’s ability to ensure that products are consistently produced and controlled to appropriate quality standards in the production of foods, pharmaceutical products, and medical devices. GMP covers all aspects of the manufacturing process, product storage and transport, serial number tracking, and lot traceability. Read More...
Enterprise 21 supports GMP through audit controls of transactions, electronic signatures, and version control with engineering change management of formulas and bills of materials. Enterprise 21 also enables forward and backward lot traceability, shelf life management, and tracking and control of dangerous and restricted items. The overriding principles of GMP include designing quality into a product and controlling all aspects of the production process and associated material flow.
Enterprise 21’s production reporting and shop floor control functionality offers discrete and process manufacturers the ability to record real-time labor and production data. Production reporting can be performed by employees in a variety of manners, including data entry with keyboards and touch-screen devices and scanning from tether-attached, handheld, and forklift-mounted devices. Enterprise 21’s production reporting and shop floor control capabilities enable efficient data entry and organization-wide access to production data, supporting inventory management, customer service, financial management, and costing processes. Read More...
Production Reporting Highlights
- Supports capture of materials, packaging, and labor consumed and finished goods produced by routing process step
- Manufacturing variances can be recorded and analyzed
- Supports separate data capture of finished goods production and inventory putaway
- Supports one-step production reporting for organizations that prefer more simplistic recording of finished goods with simultaneous backflush at standard of materials and labor consumed
- Supports recording of machine downtime and production scrap for accurate costing and root cause analysis
- Supports tracking of employee exposure to hazardous chemicals
- Supports lot tracking from ingredients through intermediates to finish goods
- Supports serial number tracking from components through subassemblies to finished goods
- Supports reporting of disassembled manufactured goods, kits, and assemblies
- Supports production recording in multiple units of measure
- Supports catch weight processing
Watch the Enterprise 21 Kitting & Assembly DemoEnterprise 21 ERP software supports kitting and assembly processes for manufacturing and distribution organizations. Kitting can be performed through a picking process or as a manufacturing process where associated labor and burden are also collected for accurate costing purposes. Read More...
In Enterprise 21, kitting and assembly processes use the establishment of an infinite-level bill of materials. Manufactured kits and assemblies also use associated routings. In the Enterprise 21 system, organizations can establish the schedule for manufactured kits and assemblies through the production planning or MRP process.
Assembly processes can either be performed within the given organization or as outside operations by a third-party company. If the assembly process is outsourced to a third party, Enterprise 21 can generate a purchase order for the assembly services performed and shipping documents for sending the raw materials and components to be consumed to the third-party assembler.
Kitting and Assembly Highlights
- Supports multi-level bill of materials
- Kitting can be performed through a picking process or as a manufacturing process where associated labor and burden are also collected for accurate costing purposes
- Supports multi-step routings for manufactured kits and assemblies
- Allows item substitutions within a kit
- Supports serial number tracking when applicable to kitted and assembled items
- Tracks associated cost to manufactured kits and assemblies
- Supports the ability to disassemble kits and assemblies for consumption of component items in other processes
Enterprise 21’s manufacturing software functionality includes complete engineering change order (ECO) processing for discrete and process manufacturers. Through the ECO process, a new version or revision of a given product’s bill of materials (BOM) or formula can be created. In Enterprise 21, the given engineering change can be routed through the organization for online review and approval for the promotion of a proposed BOM or formula to an active status. The new version of the BOM or formula would be used in material requirements planning (MRP), production scheduling, production recording, and for updated product costing. A similar engineering change process is used for the revision of production routings. Read More...
Engineering Change Orders Highlights
- Supports creation and routing of engineering change orders (ECO) through the organization for review and approval including on-line electronic signatures
- Maintains version and revision control in product development and manufacturing
- Used for bills of material (BOM) for discrete manufacturing, formulas for process manufacturing, and associated product routings
- Supports infinite notes to be associated with a given ECO
- Supports MRP planning based on applicable ECO effectivity dates on BOM’s, formulas, and routings
In conjunction with bills of materials for discrete manufacturers and formulas and recipes for process manufacturers, Enterprise 21’s manufacturing software functionality uses routings to help manage the entire production process. Routings consist of a series of steps which define the sequenced processes and work centers a given product must go through for its production. Read More...
Enterprise 21’s material requirements planning (MRP) and production scheduling processes generate work orders and batch runs based on a product’s routings. Individual routing steps define anticipated process standards, and can either be established as the amount of time to produce a given quantity of product, or as the quantity of product which can be produced per unit of time. Routings also include defined standard setup and queue times by process step.
In Enterprise 21, a product can have an infinite number of active routings defined at either the organization or facility level, with a specified rank ordering of routings. In the MRP process, Enterprise 21 uses product routines and other associated data to systemically create tentative production schedules by facility to best meet anticipated customer demand.
Routing Maintenance Highlights
- Routings support revision levels, version tracking, and effectivity dates
- Supports routing run time by operation step entered as either units per time or time per unit
- Supports standard setup and queue times by routing operation step
- Support by-products and co-products
- Supports the entry of raw materials, components, or ingredients consumed per routing step or operation
- Supports unlimited work instructions and notes by routing and individual step
- Supports subcontracted and outside third-party processing within routings
- Supports entry of labor required per routing step
- Multi-level where-used functionality enables rapid access and mass change processing
- Supports entry of inspection and packaging processes as operational steps within routings
Watch the Enterprise 21 Process Manufacturing DemoEnterprise 21’s process manufacturing software functionality supports the management of scalable batches. Companies can establish formulas and recipes with associated routings for batch production at defined standard batch sizes. Assuming a process manufacturer’s operations require variable batch size production, Enterprise 21 can scale the associated ingredients and intermediates in the formula to support the desired scalable batch size.
Watch the Enterprise 21 Process Manufacturing DemoEnterprise 21’s process manufacturing software functionality supports complete formula and recipe management. Multi-level formulas can include ingredients, intermediates, and other formulas. Through the engineering change processes in Enterprise 21, formulas can go through version revisions. Enterprise 21’s where-used functionality provides complete visibility to specific ingredients, intermediates, and formulas which are used in the production of multiple products. Through the integration of formulas and associated processing instructions and notes, process manufacturers can create recipes which are used during batch process production. Read More...
Formula and Recipe Highlights
- Supports infinite-level formulas with yielding at the top level or ingredient level and rank-ordered ingredient substitutes
- Products can have global formulas or unique facility-specific formulas
- Supports scalable batches
- Supports recipes through the integration of formulas and associated processing instructions and notes for use during batch process production
- System maintained version and revision control with a fully-integrated engineering change order process
- Formulas support nested formulas and intermediates and can have infinite notes and instructions
- Supports online review of formulas via single-level and multi-level explosion
- Multi-level where-used functionality enables rapid access and mass change to all finished goods using specific ingredients, intermediates, and nested formulas
- Formulas and recipes are easily duplicated and updated for the same product or a new product
- Formulas are pulled into work orders or batches for tracking and recording of actual ingredients consumed or backflushed at defined standards
- Supports co-products and by-products
- Supports lot control tracking, shelf life management, product grading, and hazardous materials tracking and reporting
At the heart of product definition for produced items in the Enterprise 21 ERP system are bills of material (BOM’s). BOM’s are primarily used for discrete manufacturing, assembly, and kitting processes in Enterprise 21. BOM’s can have infinite levels and include pseudos, subassemblies, and phantoms. Through the engineering change processes in Enterprise 21, BOM’s can go through version revisions. Enterprise 21 includes where-used functionality for visibility to where specific components and subassemblies are used across all products, enabling rapid mass change processing. Read More...
Bill of Materials Highlights
- Supports infinite-level bills of material (BOM)
- System maintained version and revision control with a fully-integrated engineering change order process
- BOM’s support pseudos, subassemblies, and phantoms and can have an infinite number of lines of notes
- Supports online review of BOM’s via single-level and multi-level explosion
- Multi-level where-used functionality enables rapid access and mass change to all BOM’s using a specific component material or subassembly
- BOM’s are easily duplicated and updated for the same product or a new product
- BOM’s are pulled into work orders for tracking and recording of actual components and subassemblies consumed or backflushed at standard
- BOM’s support yielding at the top level or component level and rank-ordered component substitutes
Watch the Enterprise 21 Procurement DemoEnterprise 21 features a complete supplier relationship management (SRM) software solution. Enterprise 21’s SRM software functionality includes features designed to allow the enterprise to interact with suppliers on a daily basis. Enterprise 21’s supplier relationship management software delivers (1) supplier contact management with an infinite number of contacts per supplier; (2) the establishment of preferred, approved and potential suppliers by individual facility and product; (3) supplier contracts by facility and product; (4) vendor Request for Quote (RFQ) processing, including awarding business by vendor, comparative analysis of the responses from each vendor, and the ability to have each vendor utilize a specific URL to provide their RFQ responses; (5) pricing history by supplier, including volume discounts on a currency or units purchased basis and customer or customer-product specific basis; (6) vendor rebates by product or a combination of products and customers; and (7) supplier performance management to continually track and analyze a given supplier’s ongoing performance against a series of key metrics. Read More...
Enterprise 21’s supplier relationship management software constantly monitors supplier performance based on metrics such as order fill rate, line item fill rate, on-date delivery, on-time delivery, and product quality on a purchase order and product basis. As a result, procurement personnel can review the full range of supplier information, and work with suppliers to improve overall performance. This process helps reduce the cost of products, improve the quality of received product, and reduce the likelihood of stock outages. This results in both significantly reduced internal costs and improved customer service and satisfaction.
The Enterprise 21 business management system supports fully-integrated request for quote (RFQ) processing. In Enterprise 21, purchasing personnel can create RFQ’s, select desired vendors for inclusion, distribute the RFQ’s, collect and evaluate vendor responses, and electronically send vendor award notifications. Purchasing personnel can review RFQ history and vendor performance data as part of determining which vendors to include in a given RFQ process. Vendor responses can be entered into Enterprise 21 either through manual processes or directly by the vendor via a secure e-Commerce portal over the Internet. Once the vendor has been selected, purchase requisitions and purchase orders can be created directly from the RFQ. Read More...
Online Request for Quotes (RFQ) Management Highlights
- Request for quotes can be entered online and assigned to multiple vendors
- Automatically prints quote solicitation letters to vendors
- Vendor responses are recorded, and purchase requisitions can be automatically generated when the quote is awarded to a vendor
- A given RFQ can be awarded to one or multiple vendors
- Supports online storage of each supplier’s quotation response
- Supports online review of RFQ history and vendor performance data as part of determining which vendors to include in a given RFQ
The Enterprise 21 business software solution supports import management including containerization and landed costing. Enterprise 21 enables purchasing personnel to review purchasing data and generate purchase orders for full or partial container loads. On a purchase order-by-purchase order basis, Enterprise 21 stores and tracks key information such as estimated shipment, on-board, required, and actual received dates, slip sheet cost, container ID, and vessel ID. Read More...
Relative to landed cost management, Enterprise 21 establishes of a series of landed cost elements such as import duties, drayage, tariffs, and bonding charges. At the time of purchase order generation, these estimated charges are associated with the purchase order. The actual import-related charges are entered into Enterprise 21 once known, and the associated landed costs can be rolled into the associated product costs.
Watch the Enterprise 21 Procurement DemoEnterprise 21’s procurement functionality supports both the entry of manual purchase orders and the automatic generation of purchase orders from purchase requisitions. For multi-facility organizations, Enterprise 21’s purchasing functionality can be used for centralized purchasing, facility-based purchasing, or as a combination of these methodologies. Enterprise 21 supports purchase orders for stock and non-stock items, drop shipments, and outsourced assembly. Enterprise 21 also supports blanket purchase orders and associated releases. Purchase orders, associated receipts, and vendor invoices enable three-way matching in Enterprise 21. Read More...
Purchase Order Highlights
- Supports both manual entry of purchase orders and automatic generation of purchase orders from purchase requisitions
- Each purchase order can have unlimited line items
- Supports purchases of material, products, supplies, and services
- Supports purchases of stock and non-stock items
- Supports line item-specific delivery dates
- Automatically flags past due deliveries and supports expediting and cancellation procedures
- Maintains PO history information by item
- Supports blanket purchase orders with releases
- Requisitions can generate release against blanket purchase orders
Watch the Enterprise 21 Procurement DemoEnterprise 21 ERP software supports the creation and review of online purchase requisitions. Purchase requisitions can be entered manually or automatically generated through Enterprise 21’s material requirements planning (MRP) and distribution requirements planning (DRP) processes. Purchase requisitions can be created for materials, products, packaging supplies, and services for one or multiple facilities. Read More...
Purchase Requisitions Highlights
- Requisitions may be entered manually or automatically generated from the MRP or DRP processes
- Requisition processing can utilize signature approvals
- Preferred vendors and pricing may be specified for individual products
- Purchasing representatives can select and convert requisitions into purchase orders
- Converted requisitions can generate blanket purchase order releases
- Requisitions can include service-related items
- Requisitions can initiate inventory transfers between multiple facilities
Enterprise 21’s vendor master file centralizes all key vendor information such as remit-to and mail-to addresses, contact information, payment terms, and credit limits. The vendor mast file also provides a mechanism for grouping suppliers for reporting and payment purposes. Read More...
Vendor Definition Highlights
- Vendor ID, name, and address
- Multiple contacts with associated contact information
- Contact-specific notes and activities
- Default currency
- 1099 vendor code
- Credit limit and discount terms
- Supports multiple mail-to and remit-to locations
- Vendor order lead time
- Preferred shipment methods
- Shipment complete and over shipment tolerance percentages
- Supports the attachment of documents and files
The Enterprise 21 business management system includes transportation management functionality to allow manufacturing and distribution organizations to manage their complete transportation requirements. Enterprise 21 includes the definition of carriers, lanes, contract terms, and freight rates to support load planning, freight rating, and route optimization. Enterprise 21 gathers shipment and delivery data to calculate and evaluate carrier performance. Read More...
Transportation Management Highlights
- Supports definition of carriers and their associated lanes and contract rates
- Supports freight rate shopping
- Supports freight consolidation based on load planning and optimization
- Supports dock scheduling and yard management
- Supports load tendering and associated document creation
- Stores proof of delivery details including date, time, and person who signed for shipment
The Enterprise 21 ERP system supports the use of pallet ID’s or license plates throughout the system’s warehouse management and inventory management processes. License plates can be used to identify single-product or mixed-product pallets in standard or random-pack quantities. Enterprise 21 also supports infinite-level nested license plates, which are license plates within license plates. Nested license plates can be used for creating consolidated truckload shipments where the nested license plate houses the complete shipment data and can be sent via advance shipping notification (ASN).
Enterprise 21 includes fully-integrated quality control functionality to assist manufacturers and distributors to produce and ship products that meet customer and compliance requirements. Enterprise 21 tracks QC inspection, records product grades and quality characteristics, and enables product acceptance or rejection based on inspection results. All quality control activity is available for inquiries, report generation, and audits. Throughout the entire production and distribution process, Enterprise 21 supports meticulous tracking of production quality, shelf-life timeframes, expiration dates, and lot controlled products. Read More...
Quality Control Highlights
- Supports QC results reporting for ingredients, components, and finished goods
- Supports the automatic identification of products that require inspection at time of manufacturing putaway or purchase order receipt
- Corrective actions can be initiated for items that fail QC inspection
- Manages quality sampling procedures with pass or fail quality tests
Enterprise 21 seamlessly tracks and documents all material movement and generates all accounting entries associated with intercompany transfers. Intercompany transfers can be entered manually and generated automatically by establishing the internal supply chain within the organization. Enterprise 21 tracks in-transit inventory from shipment to receipt to provide complete visibility during the transfer process. In addition, Enterprise 21 monitors and tracks transfer pricing and creates all necessary intercompany financial transactions. Read More...
Intercompany Management Highlights
- Supports consolidation of all plant information
- Supports networked multi-plant requirements processing and centralized procurement
- Supports consolidation of supply requirements across multiple sites within the time-phased requirements planning process (MRP, DRP, etc.)
- Supports recognition of forecasted or planned interplant demand
- Multi-plant availability and message review
- Created intercompany supply orders
- Supports transfer of supply orders for an item to another facility
- Supports accounting of material and transfer costs in-transit between demand and supply locations
- Supports accounting of site-specific product and location costs
- Prioritizes the hierarchy for supplying facilities
Enterprise 21’s warehouse management functionality supports manufacturers’ and distributors’ various shipping requirements from small package to LTL to full truckload shipments. Enterprise 21 seamlessly integrates with common carriers’ shipping systems, including UPS and FedEx. All shipping information and associated tracking numbers are available to customer service personnel and can be accessed via the customer’s e-Commerce account or transmitted to the customer via EDI. Read More...
Enterprise 21’s warehouse management solution provides a daily due out schedule to enable truckload consolidation, rate shopping, and route optimization. Enterprise 21’s shipping process supports lot and serial number recording, shipment of license plates, and standard form creation for packing slips, DOT documents, VICS bills of lading, and shipping cover letters.
Shipping Highlights
- Supports load consolidation
- Supports order consolidations and carrier load assignments
- Seamlessly integrated with automatic scale and manifesting systems for small package shipping, including UPS and FedEx
- Shipping information and associated tracking numbers are available to customer service personnel and can be accessed via the customer’s e-Commerce account or transmitted to the customer via EDI
- Automatically generates necessary shipping documents and labels
- Performs freight rate calculations and identifies the least cost carrier
- Enables preferred carriers to be assigned to specific routes
- Carrier load notification can be accomplished using EDI, automatic FAX of load notification report, or direct communication
- Supports yard and trailer management
- Supports interfaces to other manifesting systems, including Clippership
- Supports unship or shipment cancellation options
The Enterprise 21 ERP system supports a variety of picking methods including pick by order, pick by area, cart picking, zone picking, wave picking, and pick queue processing. Enterprise 21 enables manufacturers and distributors to have complete control over picking processes with flexible picking rules definition and selection criteria. Enterprise 21’s warehouse management system allows an organization’s picking rules to be defined differently at various times during the business day, within months and quarters, and at year end. Enterprise 21 also offers a directed picking environment which systematically balances employee work loads. Through Enterprise 21’s flexible picking methods, manufacturers and distributors can optimize their pick, pack, and ship operations. Read More...
Pick Methods Highlights
- Supports distribution of picking requirements across multiple facilities for a single order
- Supports a variety of picking methodologies including pick by order, pick by area, cart picking, zone picking, wave picking, and pick queue processing
- Allows for different picking rules to be defined at different times during the business day, month, quarter, and year
- Generates picking lists by using multiple sets of criteria including location, batch, FIFO, FEFO, employee, zone, lot, or serial number
- Supports RF-directed picking
- Supports stock rotation through the definition of picking and putaway locations and automated replenishment notifications
- Enables optimized pick, pack, and ship operations
The Enterprise 21 business software suite can perform inventory putaway in a variety of methods including fully directed, straight to stock, or dock to stock. At the time of putaway, bar code labels or license plates can be printed and applied to the product. As with other Enterprise 21’s warehouse management operations, these transactions can be performed using a keyboard or a handheld RF-enabled barcode scanner. Enterprise 21 offers a flexible inventory putaway solutions tailored to each manufacturer’s or distributor’s warehouse requirements. Read More...
Inventory Putaway Highlights
- Supports fully directed, straight to stock, or dock to stock inventory putaway methodologies
- Putaway can be recorded via standard keyboard entry and handheld RF-enabled barcode scanners
Enterprise 21’s warehouse management functionality supports the recording of incoming material receipts via standard keyboard entry and handheld RF-enabled barcode scanners. Incoming receipts can be placed into segregated inspection locations, directly into active inventory, or in cross-docking locations. In addition, product labels can be applied when such labeling has not already been included by the supplier. Read More...
For those items requiring inspection, received material can be immediately placed on hold and applicable QC personnel alerted for further action. When lot or serial tracked items are received, Enterprise 21 enforces the recording of lot and serial data at the point of receiving. Enterprise 21 can then automatically generate applicable lot and serial number labels.
Receiving Highlights
- Receiving can be performed against a single purchase order, multiple purchase orders, and when no purchase order exists
- Receiving can be recorded via standard keyboard entry and handheld RF-enabled barcode scanners
- Supplier advance shipping notifications (ASN’s) can pre-fill anticipated receiving quantities as an additional checkpoint for data integrity purposes
- Supports automatic placement of received goods on QC hold on a product-by-product basis
- Damage identification can be recorded upon receipt
- Supports immediate allocation of inventory to sales order line items through receipts from vendors and intercompany transfers
Enterprise 21’s warehouse management functionality supports warehouse optimization and worker productivity. In the Enterprise 21 system, zones, locations, and bins can be assigned to facilitate warehouse slotting, optimal inventory placement by product velocity group, and optimal pick path for improved worker efficiency. Read More...
Warehouse Configuration Highlights
- Supports definition of logical facilities within a physical facility
- Supports slotting Optimization
- Supports location mapping that takes into account zones and temperature requirements
- Supports definition of warehouse zones, locations, and bins with associated capacities
- Locations and bins can be assigned a unique storage type
- Warehouses can have a variety of different location and bins types, such as picking, non-picking, staging, dock, back stock, cart, and primary pick areas
Enterprise 21’s warehouse management functionality is fully RF and barcode-enabled. Enterprise 21 supports barcode printing on forms such as pick tickets, packing slips, and work orders, and can print labels for products, locations, and pallet ID’s or license plates. In addition to on-demand barcode printing, all major warehouse management transactions can be performed directly using handheld RF-enabled barcode scanners. When using scanning technology, Enterprise 21 can perform task interleaving, thus enabling warehouse efficiencies by directing the next highest priority task to warehouse personnel automatically. All activities are time stamped to allow for further warehouse productivity evaluation. Read More...
Wireless Warehouse and Barcoding Highlights
- Supports printing & scanning barcode labels including raw materials, finished goods, license plates, location and bins
- Supports barcode printing on all documents
- Supports barcode scanning in all warehouse operations
- Supports warehouse productivity evaluation through transaction time stamps
Enterprise 21 supports the management of material safety data sheets (MSDS). In addition to storing the given MSDS by product, Enterprise 21 can automatically print the MSDS for inclusion with the product shipment. Manufacturers and distributors can define their own MSDS rules that specify how frequently a given product’s MSDS is included with a shipment. Enterprise 21’s MSDS management helps ensure organizations have the most current safety information readily available and provides a means of maintaining strict adherence to regulatory requirements.
Catch weight processing is used by food processors and distributors to manage products where an individual item’s actual weight varies. These products would typically be sold in one unit of measure such as packages or cases though priced by weight of the products shipped. Read More...
In Enterprise 21, a product’s nominal or average weight would be defined for planning purposes. Customer sales orders would be placed for a specified number of packages or cases of the given item. During the shipping process, the actual weight of the product would be captured, and the customer would be billed based on this actual weight.
Catch Weight Processing Highlights
- Supports recording of dual units of measure for inventory, sales, and invoicing transactions
- Supports definition of a nominal or average weight per item
- Supports recording of actual weights at time of shipment
- Customers can order in one unit of measure such as packages or cases and be invoiced based on per-pound pricing
Watch the Enterprise 21 Inventory Management DemoEnterprise 21’s inventory management functionality provides superior inventory control and accuracy for manufacturing and distribution organizations. Enterprise 21 helps ensure inventory accuracy through the efficient management of the physical inventory and cycle count processes. In Enterprise 21, manufacturers and distributors can define their cycle count rules enabling the system to automatically generate recommended cycle counts. Physical inventory and cycle counts can be performed manually or with RF-enabled barcode scanners. Through the use of these physical inventory and cycle count processes, along with Enterprise 21’s overall inventory management functionality, manufacturing and distribution organizations can improve overall inventory accuracy.
Enterprise 21 supports an unlimited number of product-based attributes for product definition and inventory management. These attributes may be a shoe’s color and width or an entry door’s wood species and component dimensions. Attributes can be used throughout Enterprise 21 for sales order entry, pricing definition, requisition and work order generation, shipping, and invoicing. Read More...
When product attributes are used in conjunction with the online product configurator, Enterprise 21 prompts the user with a list of applicable product attributes and allows the user to select from this list of valid configuration options. As the user selects the various options, Enterprise 21 can dynamically generate online images of the product. Through the use of attributed inventory, manufacturing and distribution companies can simplify their product master data by eliminating the need for a separate product code for each unique combination of product attributes.
Enterprise 21’s supports the food and beverage, pharmaceutical, chemical, and consumer packaged goods industries through the tracking and online visibility of inventory shelf life and associated expiration dates. This visibility enables sales and marketing personnel to proactively move these products before their expiration. Enterprise 21 can automatically allocate inventory to sales orders and production processes on a first-expire-first-out basis (FEFO). Furthermore, retest periods can be established for shelf life-managed items so quality control (QC) personnel can reevaluate the physical properties of the given inventory. This process helps ensure compliance to regulatory requirements, protects the organization from unnecessary recalls, and helps reduce inventory costs due to product and ingredient obsolescence.
The Product Recall Readiness Self-Assessment survey consists of 12 questions requiring simple “Yes” or “No” responses. The self-assessment may be downloaded or taken on-line. A score will be assigned to your response to each question, and your cumulative score for all questions will then be determined and your recall-readiness defined by comparing your score to the maximum possible score of 100. The self-assessment is quick (it should take less that 2 minutes to complete) and can provide you with invaluable information as a starting point for defining whether or not your organization is adequately prepared for a product recall.
Click here to download the Product Recall Self-Assessment survey or click here to take the survey online .
*Please note individual survey responses will not be shared with any third party entity and will be reported only in aggregate form. Individual company identities are not maintained.
Successful product recall management is one of the most important challenges any food, beverage, medical device, pharmaceutical, or chemical company may face. With always changing and increasingly stringent FDA and USDA requirements, a product recall is a very real possibility and can have a serious impact on the daily operations of the organization. To aid manufacturers and distributors in the recall process, Enterprise 21 delivers a complete sub-module devoted to product recall management. This automated software solution includes both forward and backward lot traceability and serial number tracking, mock recall testing, establishment of recall-specific contacts for both suppliers and customers, storing of pre-defined documents and press releases associated with potential recalls, and the ability to e-mail these documents directly to the intended recipients.
Watch the Enterprise 21 Lot Traceability DemoThe Enterprise 21 ERP system provides complete lot tracking from receipt of inbound ingredient and component lots which are consumed in manufacturing and ultimately shipped out to customers. Enterprise 21 supports both forward traceability from ingredients to customer shipments, and backward traceability from customer shipments, to manufactured lots, and finally to ingredient or component receipt from suppliers. In additional to lot number tracking, the lot tracking process also includes tracking of lots’ properties, grades, and testing results. Read More...
Lot Traceability Highlights
- Supports forward lot traceability from ingredients through manufacturing processes to finished goods, which are ultimately shipped to customers
- Supports backward lot traceability from finished goods back into manufacturing processes to ingredient and component receipts from suppliers
- Supports complete chain of custody or product pedigree management and reporting
- System and procedural controls are required to provide the source and destination of a given lot to support product recalls
- Supports complete QC processes of inbound receipts and manufactured products
- Complete visibility to which vendor supplied a specific lot and which customers received a specific finished good lot
- Complete visibility to recorded lot properties for ingredients, components, and finished goods
Enterprise 21’s inventory management functionality provides complete serial number and warranty tracking. Enterprise 21 tracks serial numbers and warranty periods for components, distributed items, and manufactured goods. The system also supports the consumption of serialized components in serialized finished goods. Enterprise 21 automatically tracks whether items being serviced or returned are covered under warranty. Read More...
Serial Number and Warranty Tracking Highlights
- Supports assignment of serial numbers at time of receipt, production, or upon shipment
- Tracks serial numbers of components used in production
- Tracks serial numbers shipped to customers and those remaining in stock
- Tracks warranty information by serial number
- Tracks vendor warranty by date of receipt or date of shipment to customer
- Tracks warranty for manufactured products
- Automatically tracks whether items being serviced or returned are covered under warranty
Enterprise 21 delivers a high-degree of flexibility in the management of product units of measure. Manufacturing and distribution organizations can define global and product-specific unit of measure conversions. On a product-by-product basis, default units of measure can be defined for various types of transactions. This allows manufacturers and distributors to sell, purchase, manufacture, receive, store, and ship in any unit of measure required. Read More...
Multiple Units of Measure Highlights
- Supports unlimited global and product-specific units of measure (UOM) conversion factors
- Supports use of default units of measure and automatic conversion to alternative units of measure in transaction processing
- Supports default UOM for stocking, purchasing, selling, shipping, manufacturing, and reporting on a product-by-product and product-facility specific basis
Enterprise 21 inventory management functionality manages inventory demand and assignment through the usage of inventory commitment and allocation. When sales orders are placed in Enterprise 21, available inventory can be committed to order line items. Then, as the date of order delivery approaches, the inventory allocation process ties specific physical inventory to order line items for warehouse pick, pack, and ship processing. The allocation process would also tie specific components, ingredients, and subassemblies to manufacturing work orders for production processing. Enterprise 21’s inventory management functional flexibility enables manufacturing and distribution organizations to define a series of business rules for inventory committing and allocation processing. Through this process, organizations can uniquely-define how they manage their inventories to provide outstanding customer service. Read More...
Inventory Commitment and Allocation Highlights
- Supports inventory committing to line items during sales order entry
- Inventory allocation ties specific physical inventory to sales order line items and manufacturing work orders
- Supports allocation by lot number and serial number
- Supports configurable business rules to meet each organization’s unique inventory management requirements
- Supports immediate allocation of inventory to sales order line items through vendor receipts and manufacturing processes
Watch the Enterprise 21 Inventory Management DemoEnterprise 21 ERP’s inventory replenishment process analyzes supply and demand across multiple companies and facilities to help manufacturing and distribution organizations improve order and line item fill rates and optimize their overall inventory management performance. The inventory replenishment process considers a variety of criteria such as on-hand inventory, customer demand, and supplier lead times to calculate requirements and generate online requisitions, purchase orders, and inventory transfer requests. This process can be as automated as desired by manufacturing and distribution organizations requiring little or no manual interaction with the software. Read More...
Enterprise 21’s manufacturing requirements planning (MRP) and distribution requirements planning (DRP) processes compare available inventory with current and future demand to predict expected shortages over time. Enterprise 21 also considers existing suppliers and their associated order requirements and lead times to produce online requisitions for review and conversion into purchase orders and inventory transfers. For manufacturing organizations, Enterprise 21’s MRP process also takes into account criteria such as bills of materials, routings, and production capacity to generate a tentative production schedule.
Unlike traditional manufacturing and distribution software packages, Enterprise 21 provides more advanced processing capabilities by considering a given product’s desired safety stock, line item fill rate, and service level. These manufacturing and distribution software capabilities provide a more complete view of the inventory replenishment process, enabling greater inventory control and improved profitability.
Inventory Replenishment Highlights
- MRP and DRP processes evaluate key criteria to generate purchase requisitions and a tentative production schedule
- Supports review of purchase requisitions to generate purchase orders and inventory transfers
- Compares available inventory with current and future demand to predict expected inventory shortages over time
- Replenishment rules include minimum-maximum reorder point, safety stock levels, line item fill rate, and service level
- Supports approved suppliers, contract terms, blanket orders, and contracted purchase amounts
- Accounts for vendor lead times and order requirements
- Demand consists of customer orders and forecast which can reflect seasonal business trends
In Enterprise 21, products can be defined across the entire business or on a facility-by-facility basis. Products can be associated with multi-level product grouping hierarchies for pricing, product management, planning, and reporting purposes. Inventory management rules can be defined either as simple minimum-maximum inventory reorder points, safety stock in days of supply, line item fill rate, or service level by product or by product-facility combination. Each product can have its own associated costing method, using either average, standard, LIFO, or FIFO costing. Read More...
Enterprise 21 supports the definition of a series of product-specific properties including velocity group, product storage type, physical dimensions, standard weight, and freight class. Additionally, Enterprise 21 also allows organizations to turn on specific processes on a product-by-production basis, including lot control, serialization, production planning inclusion, automatic quality assurance, and marking the item as sellable.
Product Definition Highlights
- Multiple-level product grouping hierarchies for pricing, product management, planning, and reporting
- Define inventory management rules selecting from minimum-maximum inventory reorder points, safety stock in days of supply, line item fill rate, or service level by product or by product-facility combination
- Supports both short and long descriptions which can be used on forms and documents, including order acknowledgements, packing slips, and invoices
- UPC product codes by product and unit of measure-specific
- Can obsolete products based on a specific date or upon exhaustion of inventory
- Supports definition of product-specific properties including velocity group, product storage type, physical dimensions, standard weight, and freight class
- Supports turning on specific processes on a product-by-production basis, including lot control, serialization, production planning inclusion, automatic quality assurance, and marking the item as sellable
- Select costing method by product either average, standard, LIFO, or FIFO
TGI has partnered with Versatile Systems to deliver a route accounting and direct store delivery (DSD) solution for small and mid-market manufacturers and distributors. This partnership delivers TGI’s robust Enterprise 21 ERP software and Versatile’s Mobiquity Route system that provide a cost-effective and state-of-the-art business software solution. Read More...
The Mobiquity Route system allows route drivers to access current customer, pricing and inventory data, to create and deliver orders in the field, and immediately communicate customer visit results to the corporate data center.
Route Accounting Highlights
- Track inventory across all routes, locations, and trucks
- Ensure on-time deliveries via directed workflow software
- Make adjustments and accept returns at each stop
- Alert driver to special instructions for stop
- Get Proof of Delivery (POD) via signature capture
- Supports return of inventory off trucks at end of day
- Enables electronic DEX invoicing to meet customer-specific requirements
Through TGI’s partnership with Versatile Systems, manufacturers and distributors can receive the benefits of a fully-integrated, end-to-end enterprise system.
Enterprise 21 supports EDI processing throughout the order-to-cash and procure-to-pay processes respectively. Enterprise 21 supports common inbound transaction such as customer purchase orders and vendor invoices, and outbound transactions such as order acknowledgements, purchase orders, and invoices. Enterprise 21’s EDI processing supports both internal warehouse processes and those performed via a third-party warehouse. Read More...
EDI integration is accomplished through a combination of Enterprise 21’s internal mapping processes for data import and export in conjunction with the external EDI translation solution of the organization’s choice. In addition to being used for EDI transactions, these mapping processes are also used for legacy data migration and interfacing to external third-party systems and databases.
EDI Highlights
- Supports standard inbound and outbound EDI transaction sets
- Works in conjunction with a variety of EDI translation solutions
- Capable of accommodating standard EDI transactions and customer-and industry-specific EDI requirements
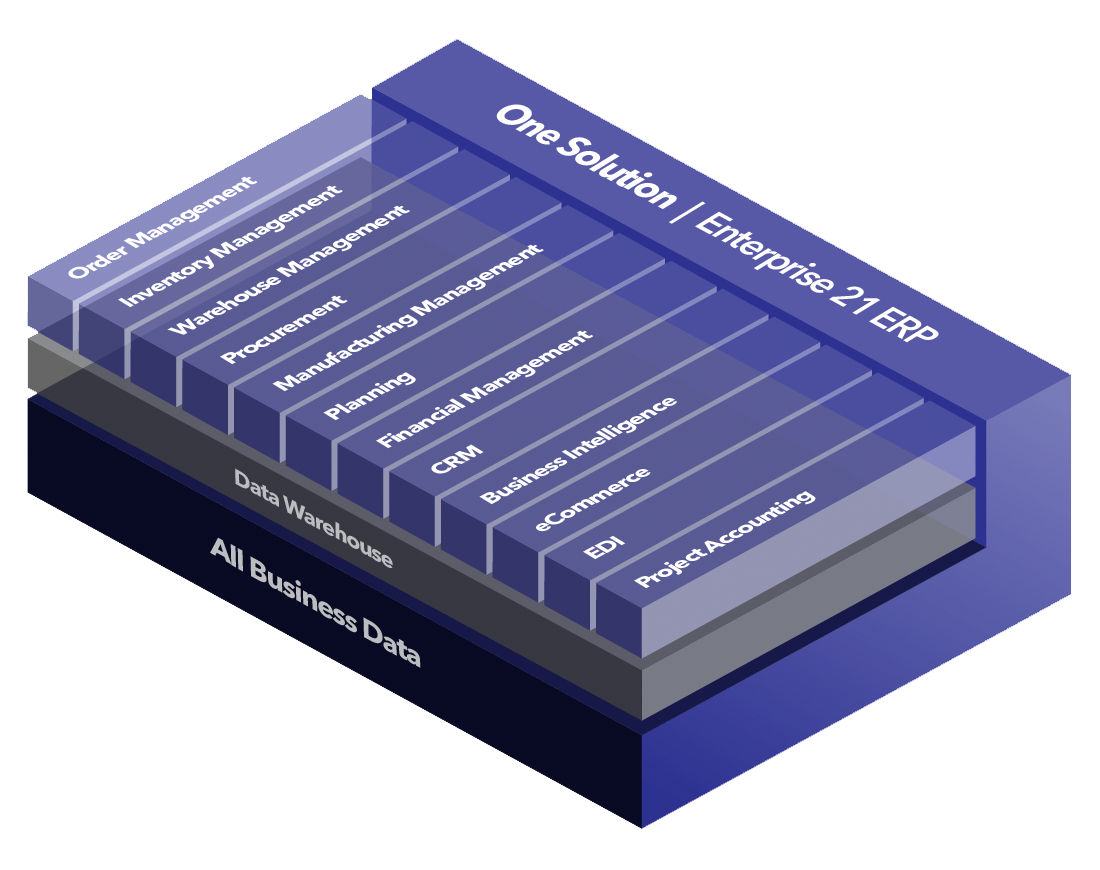
As an integral part of a manufacturing or distribution organization’s gathering and maintaining information on how it is serving its customers, Enterprise 21 ERP software monitors service levels automatically by collecting and analyzing information such as order fill rates, line-item fill rates, order change frequencies, and order cancellations. In addition, the system produces reports and management alerts to notify the organization of any anomalies in these service level metrics.
Watch the Enterprise 21 Product Configurator DemoEnterprise 21’s built-in product configurator speeds up quoting and order entry and decreases costly errors by eliminating data entry errors and non-buildable products. Read More...
The product configurator is rules-based and can be used for both parametric and features and options-based configuration of manufactured and distributed products. Enterprise 21 allows for streamlined product configuration by providing a simple drop down menu approach with immediate online graphics to show the user the configured product.
The online product configurator provides internal cost savings to manufacturing and distribution companies by reducing errors and overall time spent on configuration and estimating. This process dramatically increases the level of customer satisfaction by providing an intelligent sales force that is quick to respond to customer requests. The configurator is fully web enabled for Internet deployment and serves as an electronic expert that can help customers purchase products in a real-time.
Product Configurator Highlights
- Parametric rules-based and features and options-based configurator
- Configurator is available for use in quoting and order management
- Elimination of non-buildable products on sales orders
- Fully-integrated with manufacturing processes to create order-specific configured bill of material and associated routing
- Online illustration of configured product for review and changes
Enterprise 21’s return material authorization (RMA) processing provides a combination of flexibility and procedural controls for managing the return process. A customer return can be entered to return goods for credit, warranty repair, or replacement. This process occurs directly from the Enterprise 21’s order entry screen. The RMA process is tied directly to the receiving and accounts receivable functions for complete transactional traceability. Read More...
Return Material Authorization (RMA) Processing Highlights
- Customer items may be returned for credit, warranty repair, or replacement and have associated return reason codes
- RMA’s can be created from the original sales order and can be placed on hold pending management approval
- Returned goods can be received and inspected prior to granting customer credit
- The return process tracks lot numbers, serial numbers, and warranties when applicable
Enterprise 21’s order entry functionality supports the automatic suggestion of substitution, replacement, and complimentary products based on inventory shortages, obsolescence, and up-sell opportunities. Manufacturing and distribution companies can establish their associated substitution rules which can be global in nature or take into account customer-specific requirements for sellable items. Likewise, complimentary products can be displayed during the order entry process enabling the sales representative to present the customer the opportunity to add the items to their order. In the event a customer attempts to place an order for an item which is no longer available, Enterprise 21 automatically places the replacement item in the order entry line item. Read More...
Substitutions and Complimentary Items Highlights
- Supports product substitutions, which can either be entered automatically or by prompting the sales representative during order entry
- Supports prompting of complimentary products available for purchase based on specific products being ordered
- Obsolete products are automatically replaced with replacement products during order entry
Enterprise 21 ERP software supports the entry and online notification of product-based promotions, allowances, and rebates. Such promotions and allowances can take a variety of forms including product giveaways or order discounts. In Enterprise 21, an unlimited number of promotions can be established each of which with its own associated effectivity dates. Read More...
Likewise, an infinite number of allowances and rebates can be established and associated with a specific product or group of products. Allowances can be defined as either a percentage of the sale or as a fixed currency amount. At the time of invoicing, the Enterprise 21 system automatically calculates and accrues applicable customer rebates on an invoice line-item level. Rebate checks can be issued directly from within the Enterprise 21 system.
Promotions, Allowances, and Rebates Highlights
- Supports establishment of promotions that include product giveaways or order discounts with associated effectivity dates
- Supports an unlimited number of rebate and advertising allowance programs
- Allowances can be associated with specific products or product groups
- Allowances can be defined as either a percent of the sale or a fixed currency amount
- Supports automatic calculation and accrual of customer rebates at an invoice line-item level
- Supports rebate check issuing
Watch the Enterprise 21 Order Management DemoEnterprise 21 supports online quote entry for both existing customers and prospects. Quotes can include existing products and services and items which have never been purchased, sold, or manufactured. The quoting process supports quote routing for online approval, as well as customized quote forms. Quotes may be transmitted via email, fax, EDI, or printed and mailed. Once customer order approval is received, a quote may be converted automatically in part or in whole directly into an active sales order. Read More...
Quoting and Estimating Highlights
- Supports quotes for existing products and services and quotes with estimates for new items
- Each quote can include expiration dates and probability of customer acceptance
- Quotes may be transmitted via email, fax, EDI, or printed and mailed
- Supports pricing of quotes based on existing price sheets and authorized price overrides
- Supports routing of quotes for electronic approval
- Quotes can be converted automatically into sales orders in part or in whole
- Lost opportunities can be tracked via user defined reason codes
Enterprise 21 supports a variety of pricing structures to meet each organization’s unique requirements. The pricing management functionality supports various pricing scenarios including discount off list, contract, matrix, columnar, commodity or market, formula, unit of measure, lead-time, attribute, and volume-based pricing methodologies simultaneously. Read More...
Electronic price sheets can be established in Enterprise 21. Price sheets can have pricing with associated effectivity dates based on any of the above pricing methodologies associated with specific products or groups of products. Each given price sheet can be associated with one or more customers or groups of customers. A given product can be included on an infinite number of price sheets concurrently, with Enterprise 21 automatically selecting the given customer’s lowest applicable price.
As a fully-integrated ERP software system, Enterprise 21’s pricing functionality is used throughout the system within quoting, order management, and customer relationship management. All pricing methodologies include multi-level volume discounting. Enterprise 21’s pricing management flexibility enables manufacturing and distribution organizations to establish the appropriate pricing methodologies necessary to attract and retain customers while driving bottom-line profitability.
Pricing Management Highlights
- Supports a variety of pricing methodologies including discount off list, contract, matrix, columnar, commodity or market, formula, unit of measure, lead-time, attribute, and volume-based pricing
- Supports an infinite quantity of electronic price sheets with associated effectivity dates
- Specific products or groups of products can be on an infinite number of price sheets concurrently, with associated pricing based on any pricing methodology
- Specific price sheets can be associated with one or more customers or groups of customers
- Discounts can be established based upon a percentage, currency amount, or formula
- Market-based pricing allows prices to be set based upon a base commodity-market value plus an incremental overage specified as either a percentage or specific currency amount
- Volume discounts can be defined based on individual products or product groups, can be applied on either an annual or per order basis, and can be based on order quantity, weight, or total order value
- Effective dates on price sheets enables selection of valid pricing and entry of future pricing at any point in time
Watch the Enterprise 21 Order Management DemoA key differentiator of the Enterprise 21 ERP software suite is that it supports both available-to-promise (ATP) and capable-to-promise (CTP) processes and automated alerts. While available-to-promise processing considers existing material on hand for both purchased and manufactured items, capable-to-promise functionality also accounts for inbound purchase receipts, supplier lead times, alternative sourcing options, and raw material, production, and labor availability. During the order entry process, CTP evaluates these factors at a line-item level to calculate an accurate customer delivery date and offer alternative supplier options for raw materials or distributed items. Read More...
Available-to-Promise (ATP) and Capable-to-Promise (CTP) Highlights
- Supports automated ATP and CTP processes and alerts during order entry
- ATP processing considers existing material on hand for both purchased and manufactured items
- CTP functionality also accounts for inbound purchase receipts, supplier lead times, alternative sourcing options, and raw material, production, and labor availability
- During order entry, CTP evaluates key factors at a line-item level to calculate an accurate customer delivery date and offer alternative supplier options for raw materials or distributed items
In Enterprise 21, customers are defined at an order-from level with an unlimited number of associated ship-to and bill-to addresses. Each customer master record allows for a sales view of the account which can be used for prospecting and tracking sales-related data within CRM. Each record also provides default values for sales order entry while providing a repository of key sales and financial information. Customer accounts can be associated with a four-tiered hierarchy of customer groups used for pricing and reporting purposes. Accounts can also roll-up into corporate parents where multiple legal entities are owned by the same enterprise. Read More...
Customer Definition Highlights
- Stores basic account information such as address, unlimited ship-to and bill-to addresses, and unlimited contacts and associated contact notes
- Supports international addresses and phone numbers
- Supports key customer financial data
- Supports management of accounts and associated contacts from initial contact through initial sale and ongoing support
- Tracks key customer sales- and opportunity-related information
- Supports online inquiries of comprehensive customer information for prospecting, sales, order entry, and customer service purposes
Enterprise 21 is an ideal small business ERP software solution for growing small business manufacturing and distribution organizations. Enterprise 21 delivers a complete small business ERP solution to manage a small business’s entire operations. Unlike many stand-alone small business software solutions, Enterprise 21 is a fully-integrated small business ERP system that provides comprehensive software functionality for order management, inventory control, warehouse management, procurement, process, discrete, and mixed-mode manufacturing, accounting, and customer relationship management. TGI’s fully-integrated, small business ERP software approach eliminates the need for multiple software packages, add-ons, and duplicate data entry, providing substantial time and cost savings to the organization. Perhaps most importantly, Enterprise 21’s scalable design gives small business manufacturing and distribution companies the flexibility to grow without having to purchase additional software functionality to meet their growing business needs. TGI does not sell a downgraded or functionally-limited version of Enterprise 21, so small businesses can obtain the small business ERP software functionality required to compete with larger corporations on a global scale. Read More...
TGI's Enterprise 21 ERP software also contains a series of mapping files that allows small businesses to import data from their existing small business software packages into Enterprise 21, resulting in a faster, more cost-effective ERP implementation. Leveraging the power of Enterprise 21, small businesses can improve operational efficiency, reduce labor hours spent on duplicate data entry, and increase bottom-line profitability to gain a competitive advantage in the market with a cost-effective, all-inclusive small business ERP software solution.
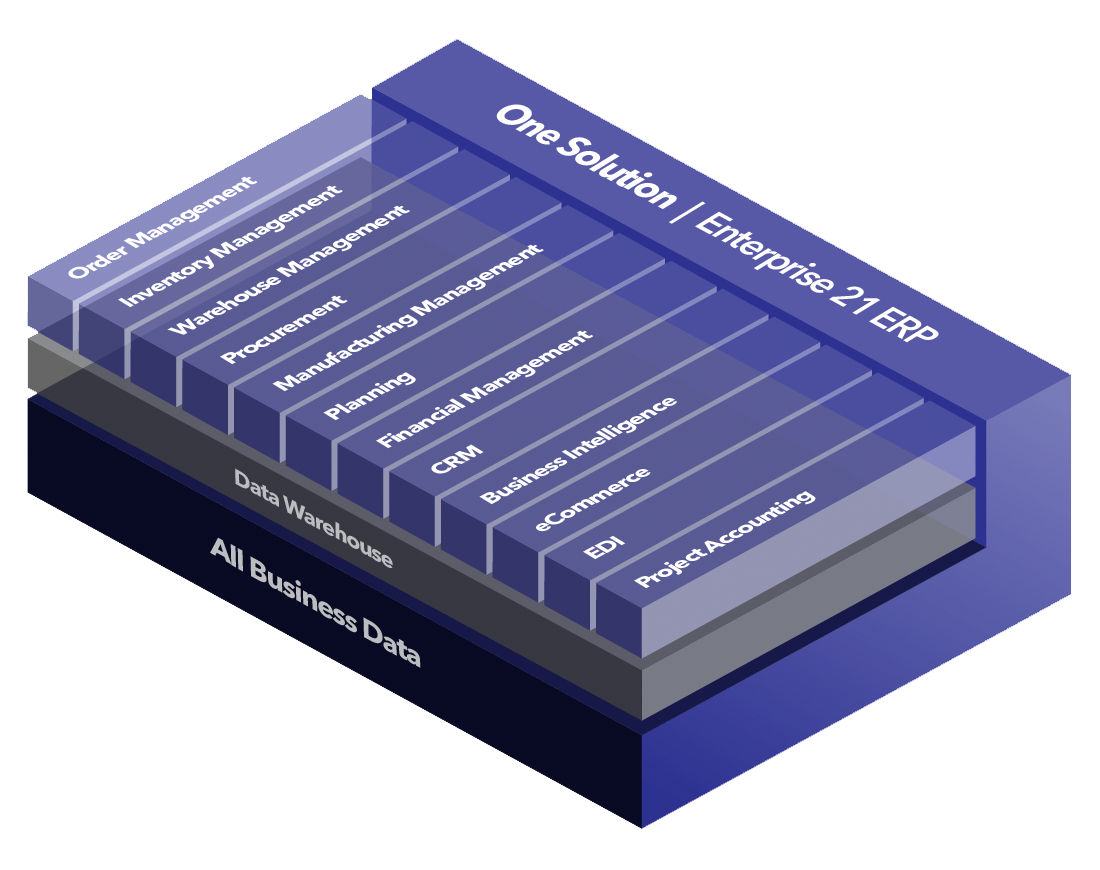
Enterprise 21 ERP software is a fully-integrated business management solution for small and mid-market manufacturers and distributors. Enterprise 21 is completely developed, implemented, and supported directly by TGI. The Enterprise 21 ERP software suite integrates with third-party applications to support organizations’ complete business needs. Read More...
Enterprise 21’s underlying architecture is flexible and configurable by design, enabling organizations to implement the system to meet unique business process requirements across a variety of manufacturing and distribution industries to achieve operational gains and a competitive advantage.
Enterprise 21 is designed to support a variety of deployment methods and infrastructure options, with complete system administration functionality to support its initial setup and ongoing usage. Enterprise 21 can be deployed in thin-client mode, thick-client mode, or as a combination of these methods using any ODBC-compliant database.
Enterprise 21’s superior breadth and depth of functionality, architectural flexibility, and scalable design allow small and mid-market manufacturers and distributors to implement and continue to run Enterprise 21 as their businesses grow and evolve while achieving new levels of operational productivity and profitability.
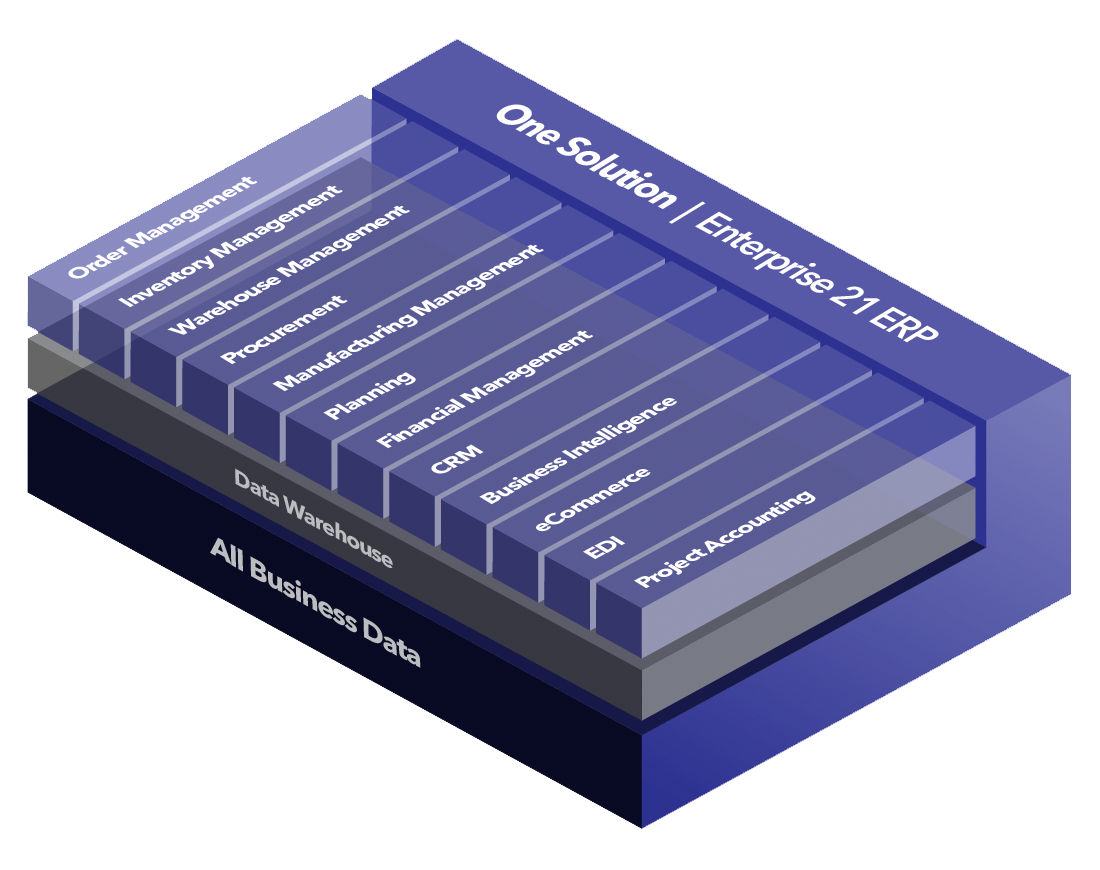
TGI has partnered with ADP to a superior human resources solution offering to small and mid-market manufacturers and distributors. This partnership delivers TGI’s robust Enterprise 21 ERP software and ADP’s advanced payroll and HR solutions that provide a cost-effective and state-of-the-art business software solution. Read More...
Human Resources and Payroll Highlights
- Web-based payroll, HR and benefits administration solutions
- Comprehensive, web-based time & attendance service
- A full suite of additional administrative services including:
- Wage garnishment processing
- Employee self service
- Background screening
- 401k administration
- Tax credit services
TGI and ADP Offer a Powerful Workforce Management Solution
- Control benefits costs
- Avoid unnecessary benefit and premium payments
- Reduce the cost of benefits administration and communication
- Minimize time employees spend managing personal benefits on the job
- Help to ensure maximum value of company-spent benefit dollars
- Improve employee retention
- Attract and select quality people
- Improve the career management process
- Improve performance management systems
- More effective salary and compensation management
- Improve employee satisfaction
- Improve organizational communications
- Improve tax and regulatory compliance
- Minimize tax liability and maximize tax savings
- Decrease business and professional risk (non-tax)
- Help you focus on running your business
- Reduce labor costs
- Reduce direct labor costs
- Improve project and product cost knowledge
- Reduce indirect expenses associated with HR and accounting
- Increase productivity
Enterprise 21's project accounting software solution provides flexible project management tools while maintaining a detailed account of a project’s costs and associated revenue. Enterprise 21 automates project costing, scheduling, and billing for both product and service items. Enterprise 21’s project accounting functionality facilitates the tracking of all items within a given job by leveraging the system’s ability to comply with a given contract’s terms while tracking project profitability. Enterprise 21 project accounting allows users to track all aspects associated with complex and multi-phase projects across a wide range of industries. Read More...
Project Accounting Highlights
- Supports definition of job templates
- Supports breakdown of projects by phases, steps, and tasks
- Supports tracking of purchased items and expenses, material, labor, and burden costs, and non-manufacturing-related employee time and expenses
- Allows sales orders and purchase orders to be associated with a project
- Tracks customer invoices and vendor payments made to a given project
- Tracks project budget versus actual
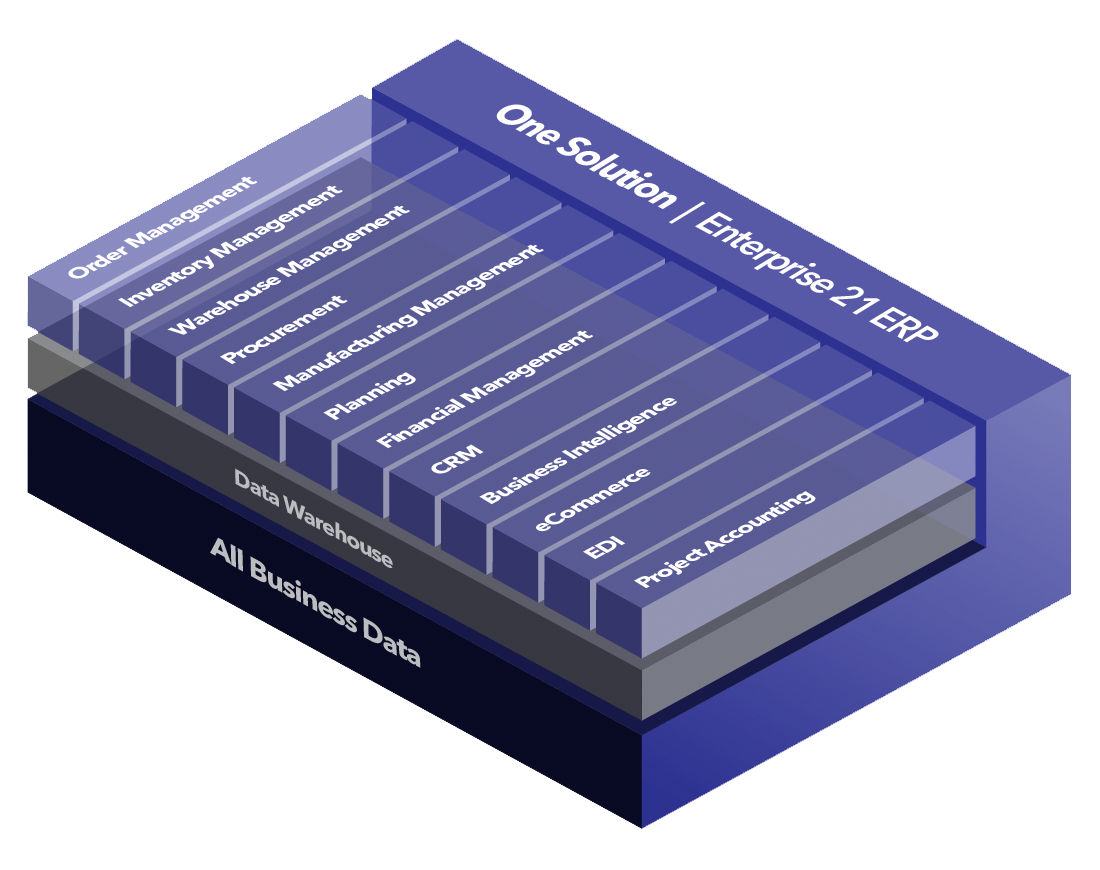
TGI’s e-Commerce solution is fully-integrated with the Enterprise 21 application. Enterprise 21 supports secure, Web-based business-to-business (B2B) and business-to-customer (B2C) transactions. Employees, dealers, suppliers, and customers can all access Enterprise 21’s data securely via the Internet. From supplier RFP responses and online customer ordering to dealer and outside sales personnel inquiries regarding inventory availability and shipment tracking, Enterprise 21 provides secure, Web-based access that extends operational activity beyond the manufacturing plant and distribution center. Read More...
Enterprise 21 e-Commerce Highlights
- Supports B2B and B2C transactions via integrated shopping cart
- Provides secure online access for employees, consumers, dealers, and suppliers
- Supports product inquiries, pricing, purchases, and transaction history
- Integrates with existing Web site look and feel to front-end Enterprise 21
- Supports automated request for proposal distribution, supplier responses, and award notification
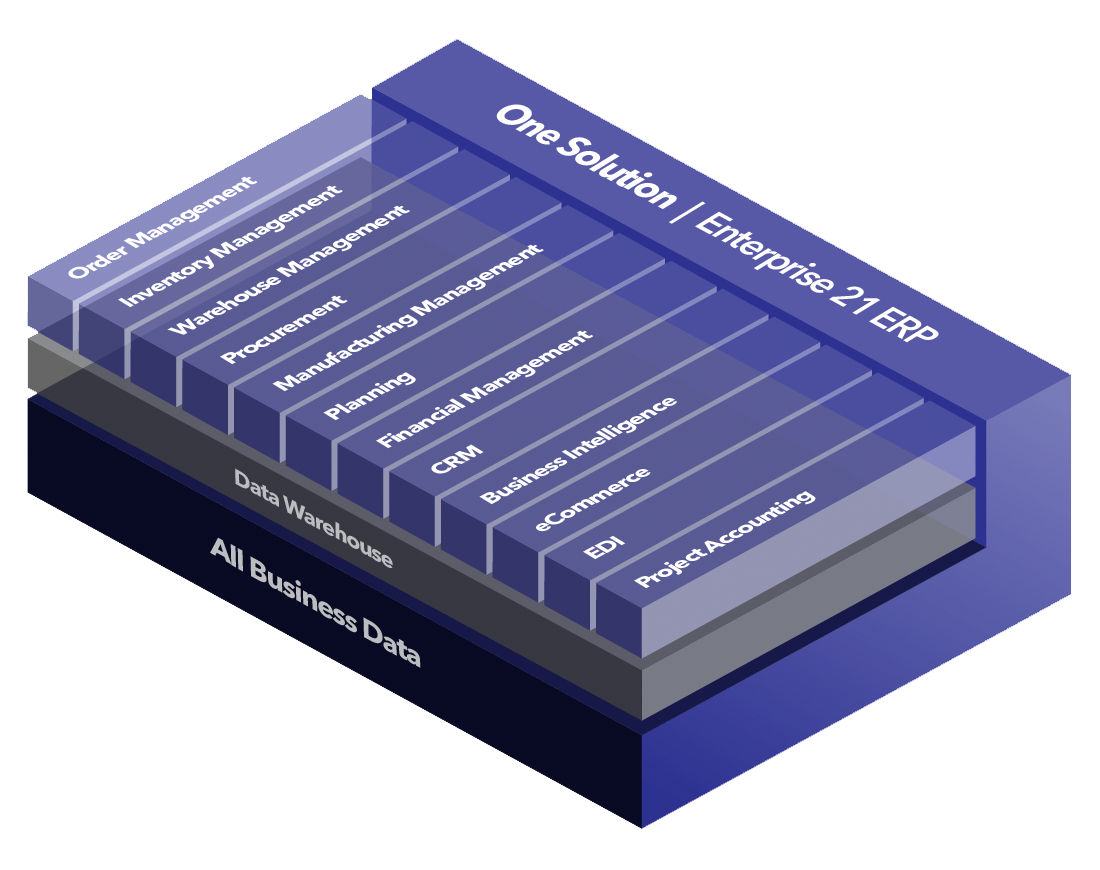
Enterprise 21’s business intelligence functionality is fully-integrated within the application. The business intelligence (BI) functionality provides real-time information presented in a variety of manners that best meet individual users’ preferences. Read More...
At the heart of Enterprise 21’s business intelligence system is the fully-integrated decision support functionality. Through the decision support system, TGI customers can deploy dashboards and key performance indicators (KPI’s). Additionally, Enterprise 21 users can drill-down on the data presented in the decision support system to perform analytical analysis. The data presented in the decision support system is populated automatically from transactional data in Enterprise 21.
In addition to KPI’s and dashboards, Enterprise 21 includes workbenches which are consolidated views of a variety of associated data for review and action. Workbenches are created without modification to application source code. From a workbench, users can navigate to all other areas in the system to perform transactions, run reports, or drill-down to more detailed data.
Furthermore, Enterprise 21 includes hundreds of standard reports and forms which were created by TGI using Crystal Reports. Crystal Reports can be used to customize standard documents and create customer-specific ad-hoc reports and forms.
Through this combination of functionality, Enterprise 21 delivers a powerful and flexible business intelligence and reporting solution to manufacturing and distribution companies.
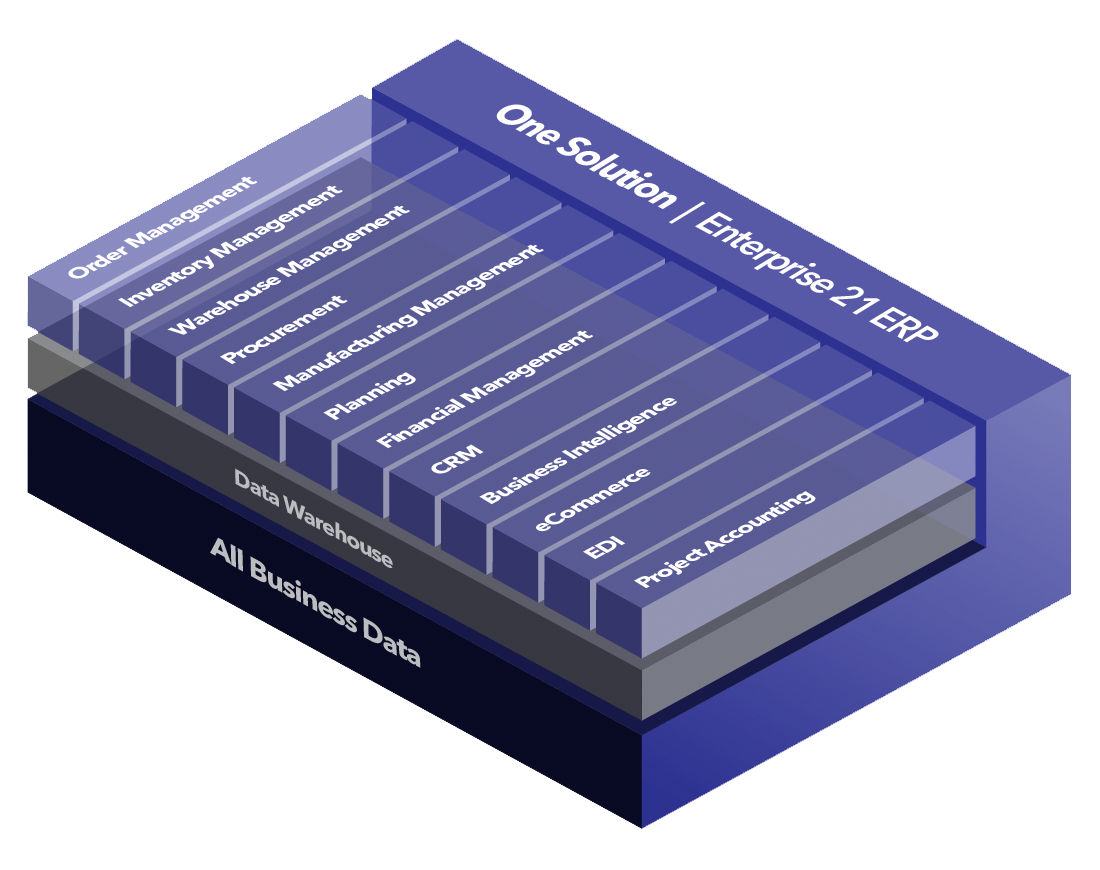
Enterprise 21’s 360° CRM functionality provides a fully-integrated approach to customer and prospect interaction. Unlike most ERP systems on the market today, which have CRM software as separate module, Enterprise 21 CRM functionality is leveraged throughout the entire Enterprise 21 software suite. In doing so, Enterprise 21 offers a comprehensive 360° view of manufacturing and distribution companies’ customers and prospects. Read More...
At its core, Enterprise 21 is based on a management-by-exception philosophy that monitors and provides alerts. These alerts provide sales and customer service personnel proactive tools to initiate action and communicate status to their customer contacts. Furthermore, Enterprise 21 ERP software monitors recent customer purchases and compares the data to the customer’s order frequency to alert appropriate personnel when there is a decline in activity, prompting proactive communication with the customer.
Enterprise 21’s CRM functionality integrates with the complete Microsoft Office Suite including Microsoft’s Outlook and Exchange, Word, Excel, and MapPoint, allowing one-click access to email, document mail merge, data export and manipulation, and customer and prospect mapping.
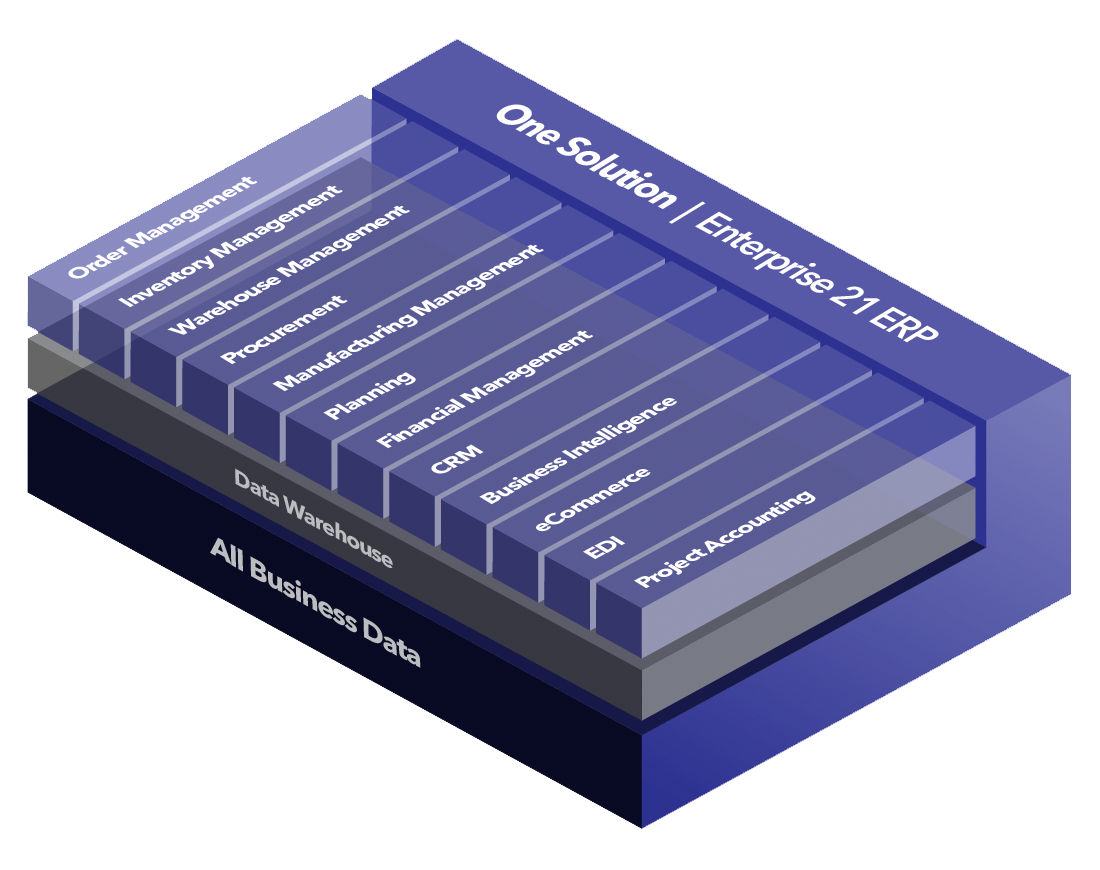
Enterprise 21 offers fully-integrated ERP accounting software tools to manage all aspects of an organization’s financial management and compliance requirements. Enterprise 21 provides a complete set of ERP accounting software functionality that is both comprehensive and scalable to manage a variety of businesses that range from small businesses to large, multinational corporations with multiple legal entities and divisions. Read More...
In addition to standard general ledger, accounts payable, and accounts receivable functionality, Enterprise 21 includes a robust financial report writer. Most importantly, Enterprise 21’s ERP accounting software functionality is fully-integrated with the entire Enterprise 21 ERP application, including inventory management, warehouse management, purchasing, order processing, manufacturing and planning, CRM, business intelligence, and e-Commerce, eliminating the need for duplicate data entry in multiple software packages and streamlining the organization’s financial management and accounting operations.
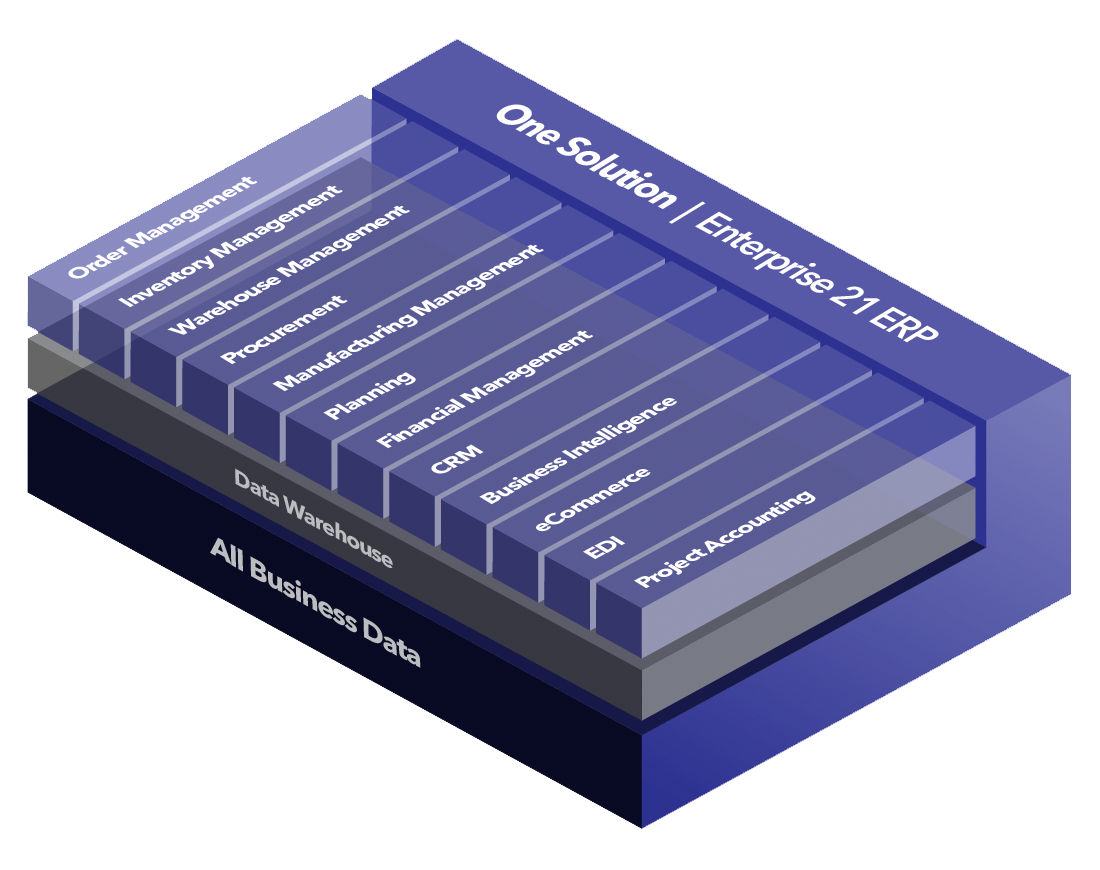
Enterprise 21 business management software supports fully-integrated planning processes for single and multi-facility manufacturing and distribution organizations. The planning process begins with customer demand, which is comprised of sales orders and forecasts. Read More...
Manufacturers can run the material requirements planning (MRP) process which generates a series of purchase requisitions and tentative production schedules. Buyers and material planners can review the purchase requisitions to generate purchase orders and intercompany transfers, while manufacturing planners can review the tentative production schedules to generate final production schedules.
Distributors can run the distribution requirements planning (DRP) process which generates purchase requisitions to be reviewed and converted into purchase orders and intercompany transfers. For multi-facility organizations, Enterprise 21’s DRP process can be used for centralized purchasing, facility-based purchasing, or as a combination of these methodologies.
Both the DRP and MRP processes enable distributors and manufacturers to establish realistic and achievable material and manufacturing plans to readily meet customer demand, improve customer service, decrease material and operational costs, and drive business profitability.
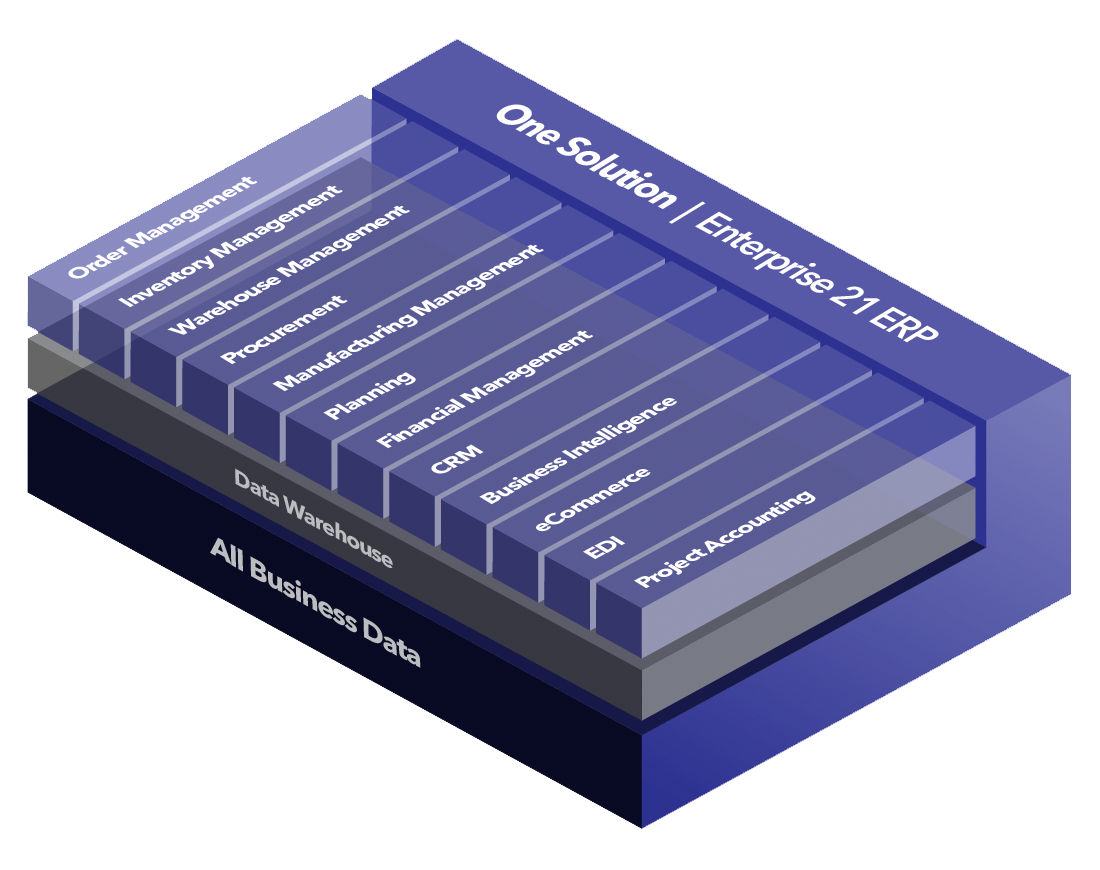
Enterprise 21’s manufacturing management software functionality supports process, discrete, and mixed-mode manufacturers engaged in make-to-stock, make-to-order, assemble-to-order, configure-to-order, and repetitive manufacturing processes. The Enterprise 21 system provides superior functionality for managing advancing planning, production scheduling, material requirements planning, and production reporting. Read More...
Additionally, distribution organizations can leverage Enterprise 21’s kitting and assembly functionality to manage their internal and outsourced manufacturing requirements to deliver superior value-added services to their customers.
Enterprise 21’s manufacturing management software functionality provides a flexible solution to meet a variety of manufacturing environments and associated industry compliance requirements. Enterprise 21 delivers improved order fill rates while reducing manufacturing and inventory carrying costs. This is accomplished through Enterprise 21’s fully-integrated manufacturing planning and scheduling functionality, streamlined production reporting, and robust quality control processing.
The Enterprise 21 ERP software suite delivers the end-to-end functionality required by process and discrete manufacturers, including manufacturing, inventory, warehouse, order, procurement, and financial management in a complete, fully-integrated software solution.
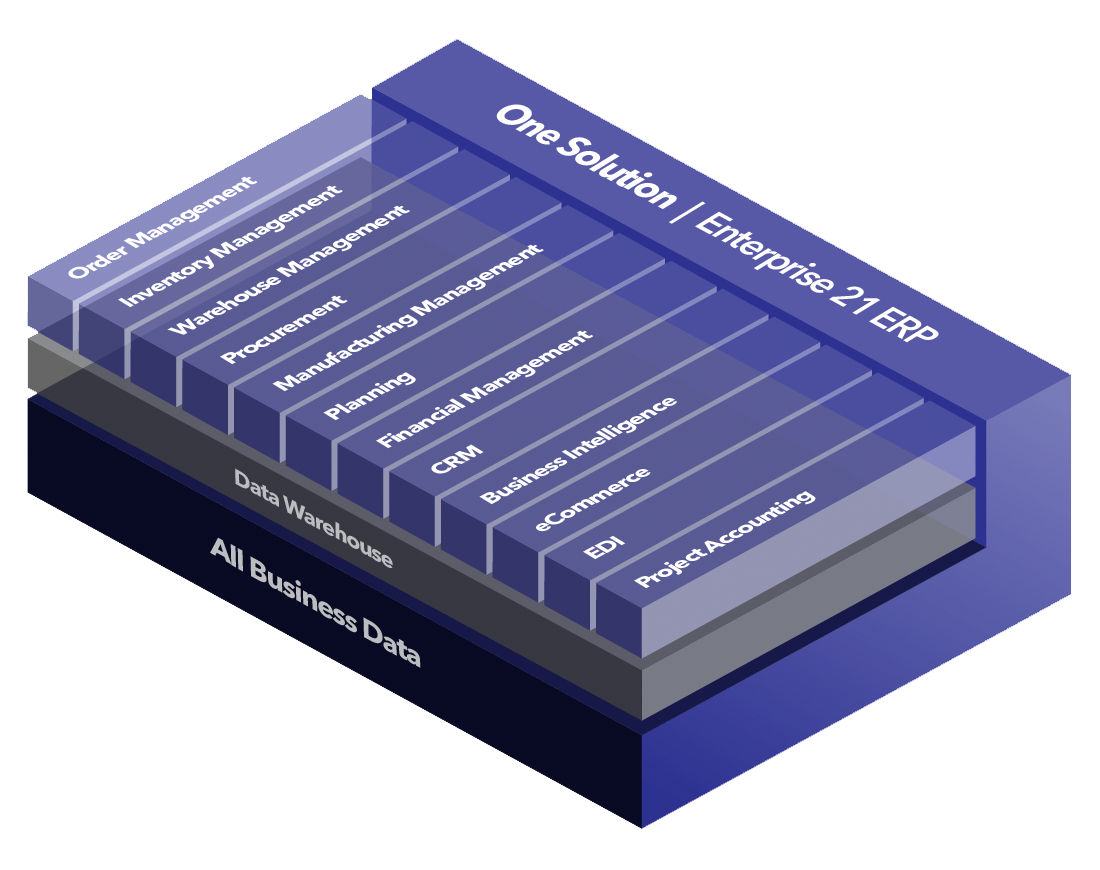
Enterprise 21’s procurement functionality enables single and multi-facility manufacturing and distribution organizations to manage all purchasing and sourcing activities in a single, fully-integrated ERP software solution. Enterprise 21 processes requisitions and purchase orders in real-time that tie directly to inventory receipts and vendor invoices to enable three-way matching. Purchase requisitions and purchase orders can be entered manually or automatically generated through Enterprise 21’s material requirements planning (MRP) and distribution requirements planning (DRP) processes. In addition, Enterprise 21 supports import management including containerization and landed costing. Enterprise 21’s procurement functionality tracks and analyzes vendors’ ongoing performance against a series of key metrics to reduce procurement-related costs and improve business profitability.
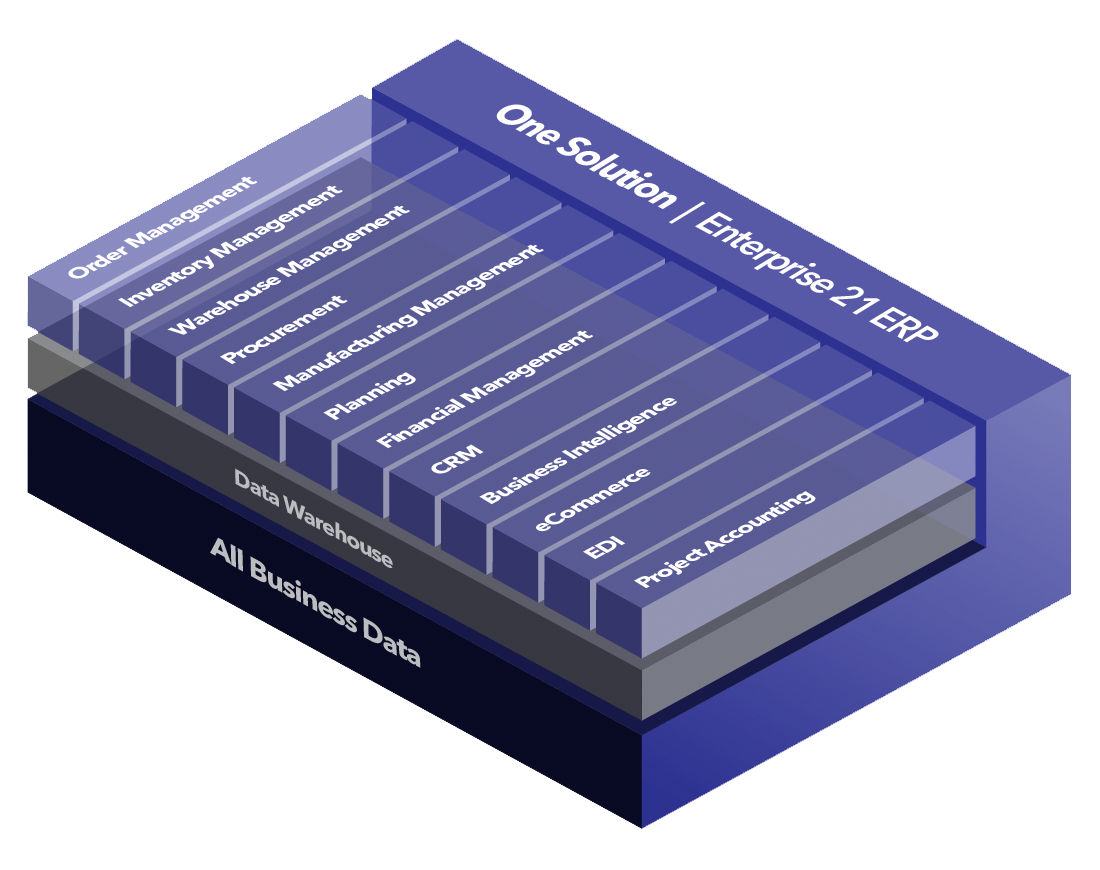
Enterprise 21 includes complete, state-of-the-art warehouse management functionality that supports standard processes such as receiving, putaway, picking, replenishment, and shipping. The warehouse management functionality manages both single and multi-warehouse operations with transactions being performed both by keyboard and handheld and forklift-mounted RF-enabled barcode scanning devices. The warehouse management functionality is fully-integrated with the complete Enterprise 21 ERP suite, including purchasing, manufacturing, inventory, and financial management to provide a complete end-to-end solution for manufacturing and distribution organizations. Read More...
While optimized picking can be performed with traditional paper-based processes, greater productivity can be derived through Enterprise 21’s directed picking and paperless task-interleaving processes. Enterprise 21 manages and tracks the complete flow of material through the entire organization, from receipt and putaway of material, through production and kitting, and eventual picking, packing, and shipping to customers with complete lot traceability and serialization tracking. Enterprise 21 also automates the management of other warehouse operations such as physical and cycle counts, vendor returns, license plating, and labor allocation and optimization.
Enterprise 21 ERP software provides the tools necessary for efficient and productive manufacturing and distribution operations. With Enterprise 21, organizations can improve their inventory accuracy, inventory turns, and customer service.
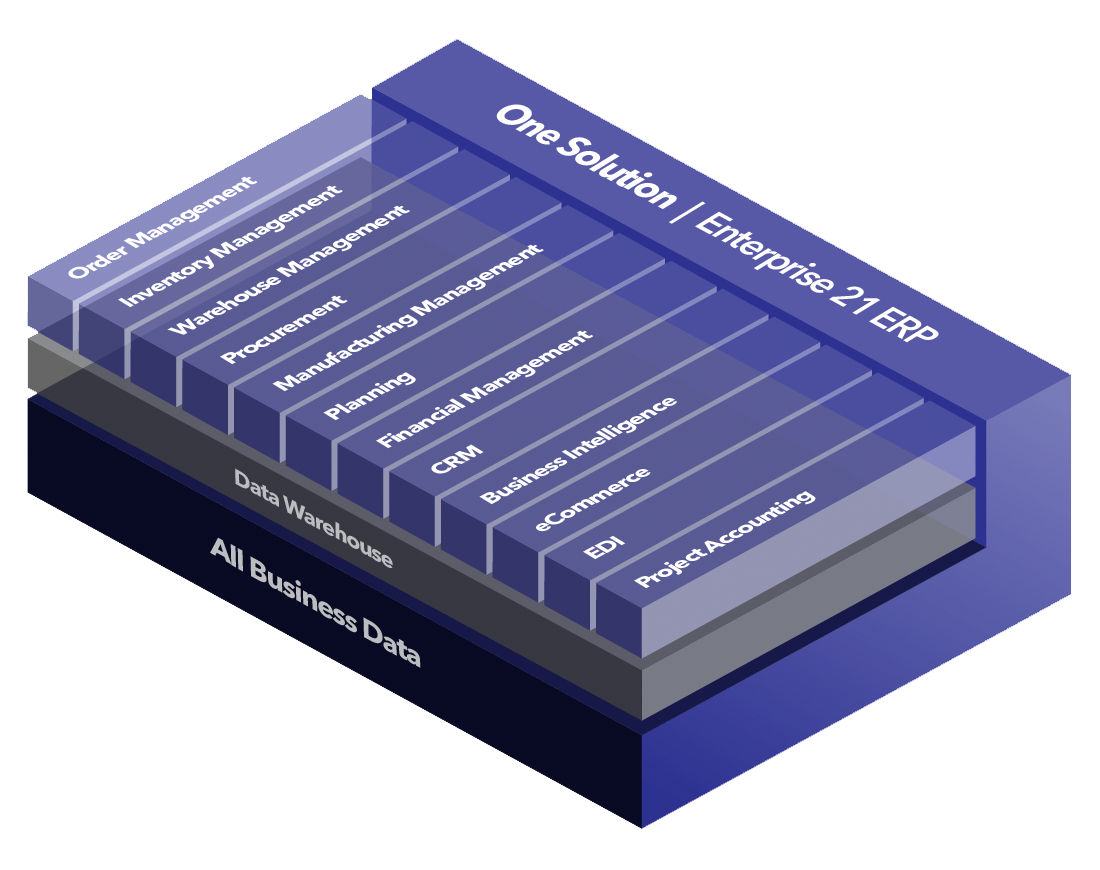
At the heart of Enterprise 21 is a robust inventory management system that provides complete control over all inventory-related activities for manufacturing and distribution companies. Enterprise 21 contains powerful functionality for manufacturing and distribution organizations to improve inventory accuracy, inventory turn rates, and order and line item fill rates. Read More...
Enterprise 21’s inventory management functionality includes paperless warehouse management, multiple inventory locations, flexible units of measure with automated conversions, physical inventory counts, cycle counts, and complete lot and serial number tracking. Enterprise 21’s inventory management is fully-integrated with the entire Enterprise 21 software suite.
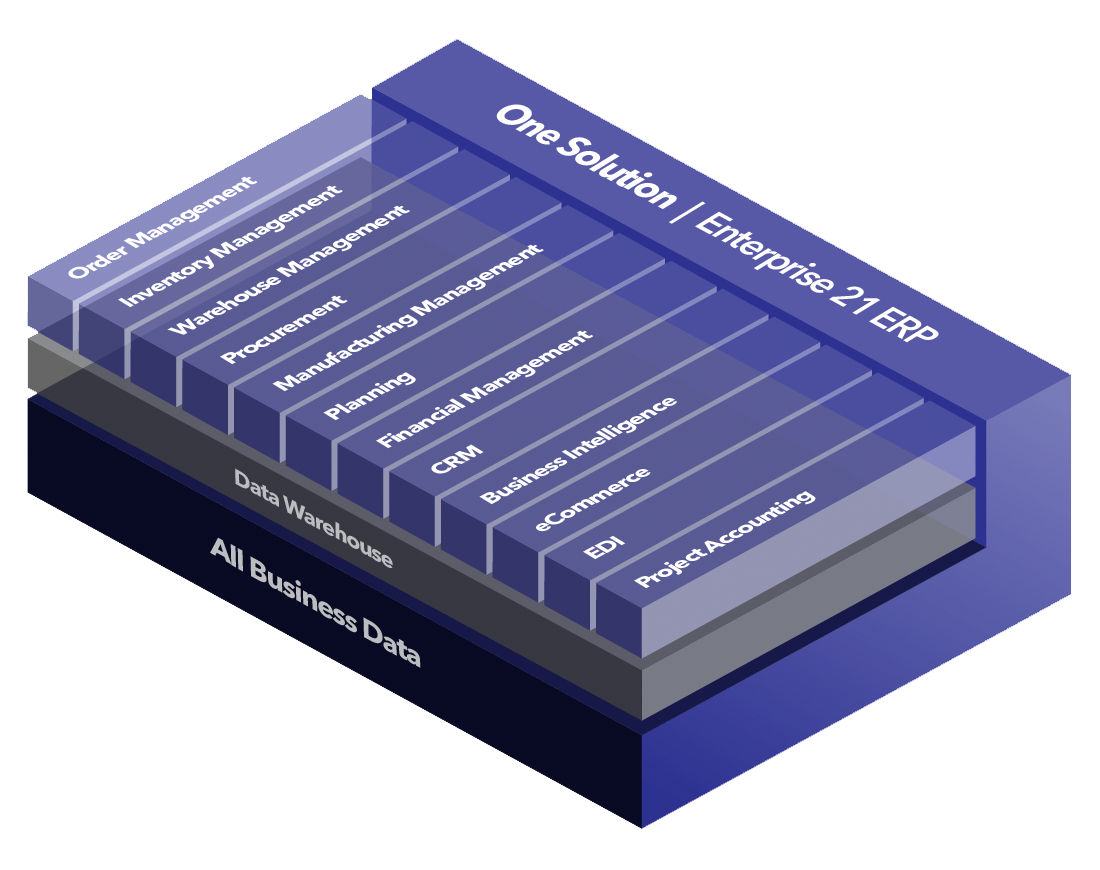
Manufacturing and distribution organizations leverage Enterprise 21’s powerful sales order management functionality to provide superior customer service. Enterprise 21 is designed to accommodate order entry processes in both B2B and B2C order entry environments. Enterprise 21 can manage regular sales orders, drop shipments, blanket orders, recurring orders, group orders, and counter sales. In addition to traditional order entry, Enterprise 21 also accommodates Web orders, route accounting management, and incoming and outgoing order-related EDI transactions. Read More...
Enterprise 21’s order management supports an infinite number of order line items, which can include stock, non-stock, and direct shipped items. In addition, the order entry process supports samples, kits, and configured products.
A key differentiator of the Enterprise 21 ERP software suite is that it supports both available-to-promise (ATP) and capable-to-promise (CTP) processes and automated alerts. During the order entry process, CTP evaluates key factors at a line-item level to calculate an accurate customer delivery date and offer alternative supplier options for raw materials or distributed items.
From the order entry screen users have one-touch access via hot buttons to any other associated information in Enterprise 21. These hot buttons can be defined on a user-by-user basis to meet the unique needs of an organization’s sales and customer service personnel.
Sales and customer service personnel can view the order status directly on the order entry screen throughout the entire order life cycle in real-time. From entry to inventory committing and allocation, through picking and shipping, Enterprise 21 provides interactive alerts and notifications for manufacturers and distributors to manage order inquiries and order changes.
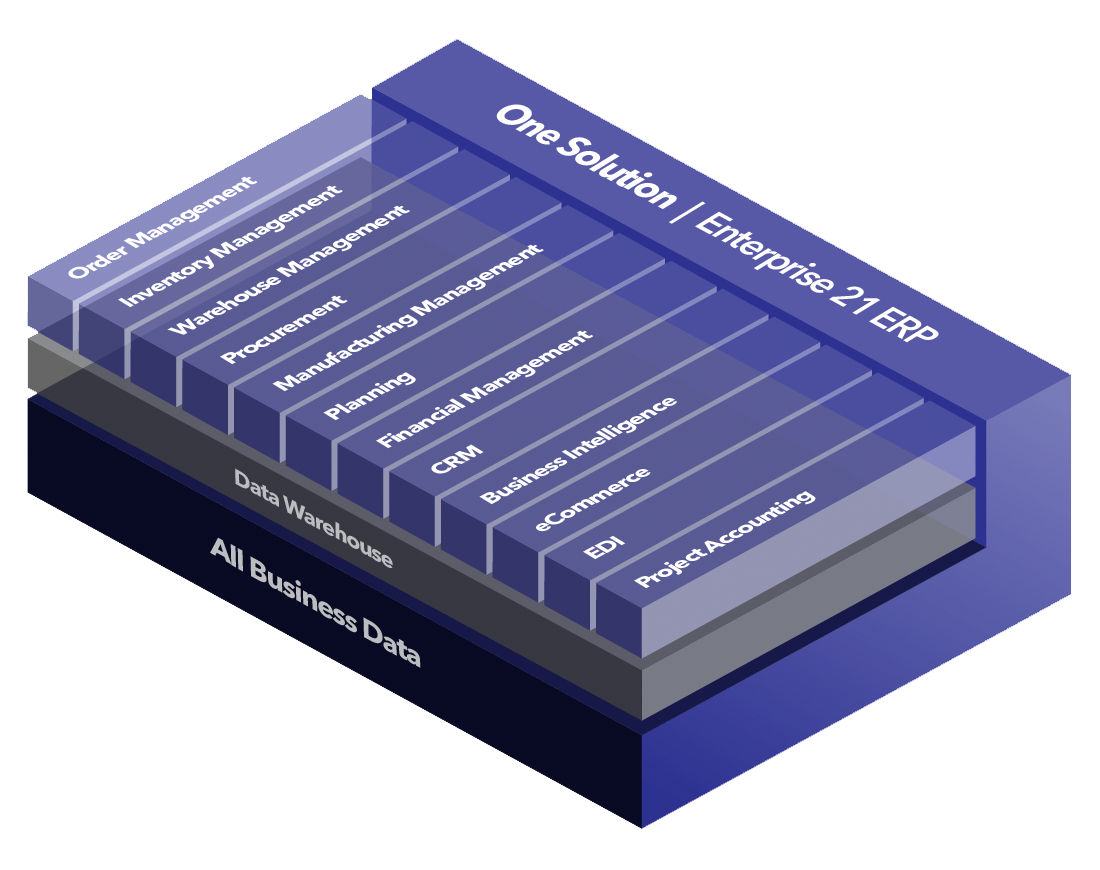
Enterprise 21 ERP is a web-based ERP system for small and mid-market manufacturing and distribution organizations. Designed as a fully-integrated, end-to-end web-based ERP application, Enterprise 21 ERP delivers the comprehensive enterprise-level software functionality required to facilitate industry best practices while serving as the backbone to manage the enterprise’s complete business operations. Read More...
As a web-based ERP system, Enterprise 21 ERP delivers fully-integrated sales order management, inventory control, warehouse management, procurement, manufacturing management, advanced forecasting and planning, financial management, customer relationship management (CRM), business intelligence (BI), e-Commerce, and project accounting software functionality in a single ERP system. From CEO’s, CFO’s, and COO’s, to warehouse managers, sales representatives, and customer service personnel, the Enterprise 21 ERP application provides the software functionality required to integrate the enterprise on a single ERP software platform. Furthermore, Enterprise 21’s underlying, web-based application architecture is flexible and configurable by design, enabling organizations to implement the ERP system to meet their unique business process requirements.
Unlike many ERP systems on the market, the Enterprise 21 ERP application is developed, sold, implemented, and supported exclusively and directly by TGI. This enables us to deliver direct, unsurpassed web-based ERP application functionality and ERP implementation services to our customers. Leading manufacturers and distributors select the Enterprise 21 ERP system to streamline business operations, increase bottom-line profitability, and gain a strategic competitive advantage. Discover the Enterprise 21 ERP system.
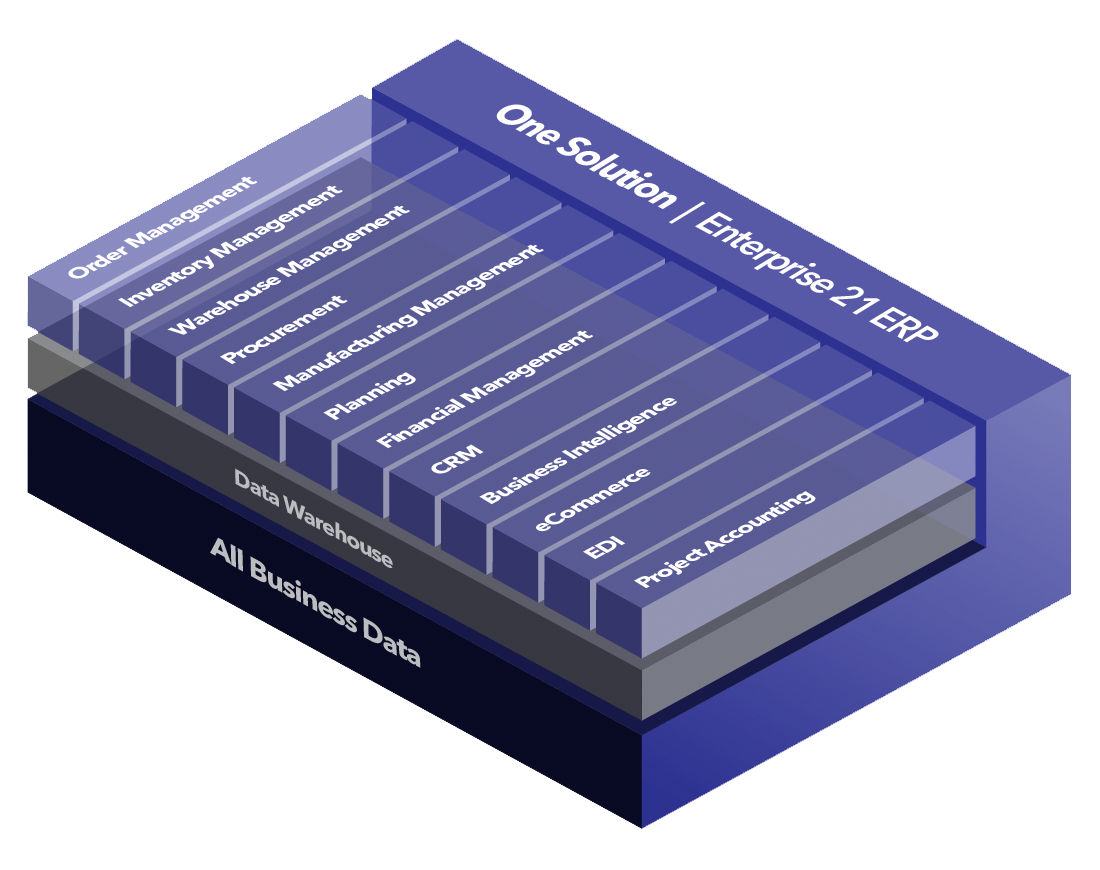